The core principle of converting waste plastic to fuel is to decompose high molecular polymers into small molecular hydrocarbon compounds through chemical/thermal conversion process. The current mainstream technologies include pyrolysis, catalytic cracking and alcoholysis.
Mingjie Group focuses on the manufacture and research of pyrolysis technology and pyrolysis equipment. Our pyrolysis plants have been widely used in plastic pyrolysis projects in many countries, such as China, the United States, Canada, Australia, the Philippines, Thailand, South Korea, Peru, South Africa, Czech Republic, Romania, Pakistan.
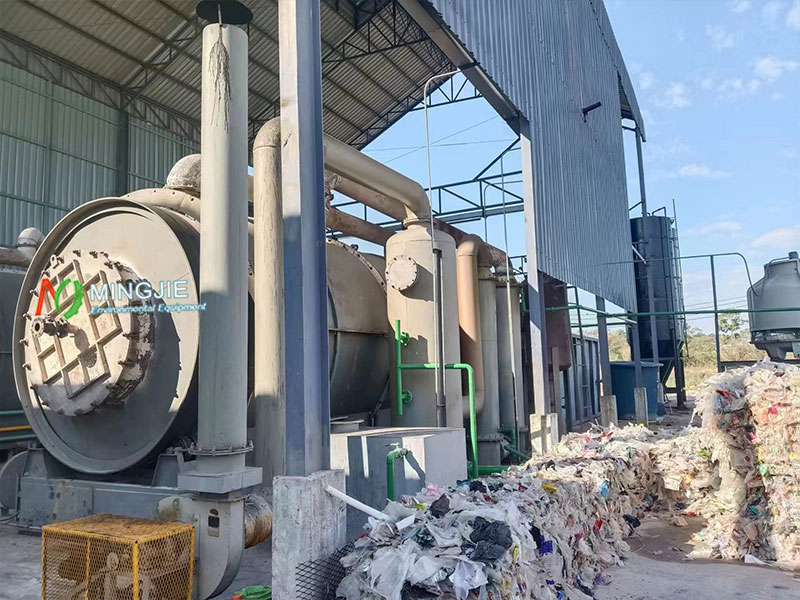
Pyrolysis of Waste Plastic to Fuel
The plastic waste pyrolysis process is a complex, simultaneous and continuous chemical reaction process. The pyrolysis reaction includes complex chemical reactions, such as organic bond breaking and isomerization. In the plastic to fuel pyrolysis process, there are two trends of change in the intermediate products. On the one hand, they are cracked from large molecules to small molecules and even gases, and on the other hand, they are polymerized from small molecules to larger molecules.
Pyrolysis reactor heats waste plastics (usually 350-550°C) in an oxygen-free or low-oxygen environment, breaking their carbon chains to produce synthetic gas, liquid (fuel oil) and solid (carbon black).
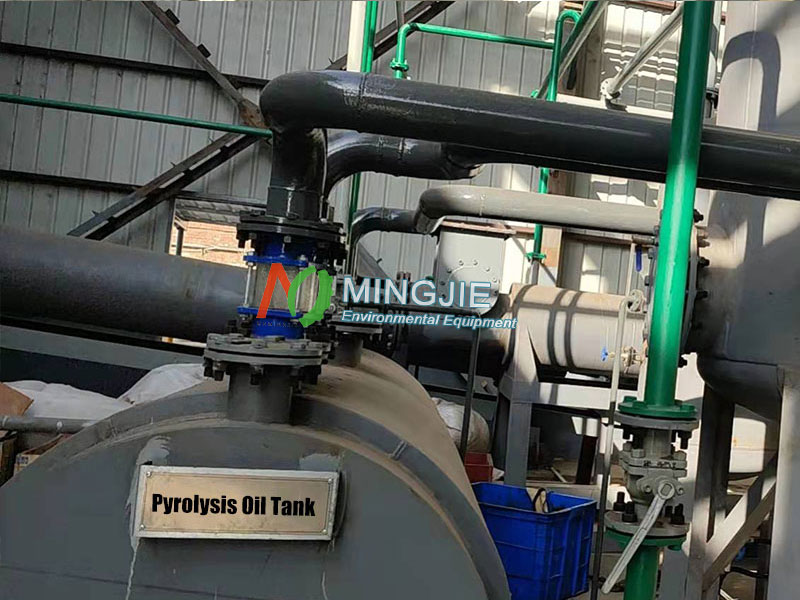
Characteristics of Plastic To Fuel Pyrolysis
Plastics of different materials have significantly different pyrolysis characteristics.
- Polyethylene (PE) and polypropylene (PP): The polyethylene pyrolysis temperature is relatively high (above 400°C). The yield of pyrolysis plastic to fuel oil can reach more than 80%, mainly producing alkanes and olefins.
- Polystyrene (PS): The polystyrene pyrolysis oil is mainly polycyclic aromatic hydrocarbons, with a yield of about 90%.
- Polyethylene terephthalate (PET): It needs to be converted by alcoholysis or catalysis, and cannot be converted by pyrolysis plant.
Plastic Pyrolysis Machine Application
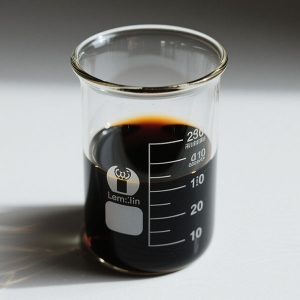
As a key technical equipment for solid waste recycling, waste plastic to fuel pyrolysis equipment plays an increasingly important role in the concept of circular economy.
Application in Energy Field
In the energy field, waste plastic to fuel pyrolysis plant has become a new idea to solve energy shortages. After pyrolysis treatment, waste plastics can be converted into fuel oil and combustible gas.
Plastic pyrolysis oil can be used as fuel for industrial boilers and kilns, replacing some traditional fossil fuels. Plastic pyrolysis oil effectively reduces dependence on traditional energy sources such as coal. This not only saves energy costs, but also reduces carbon emissions.
Synthetic gas can be directly used for heating or power generation to supplement energy supply.
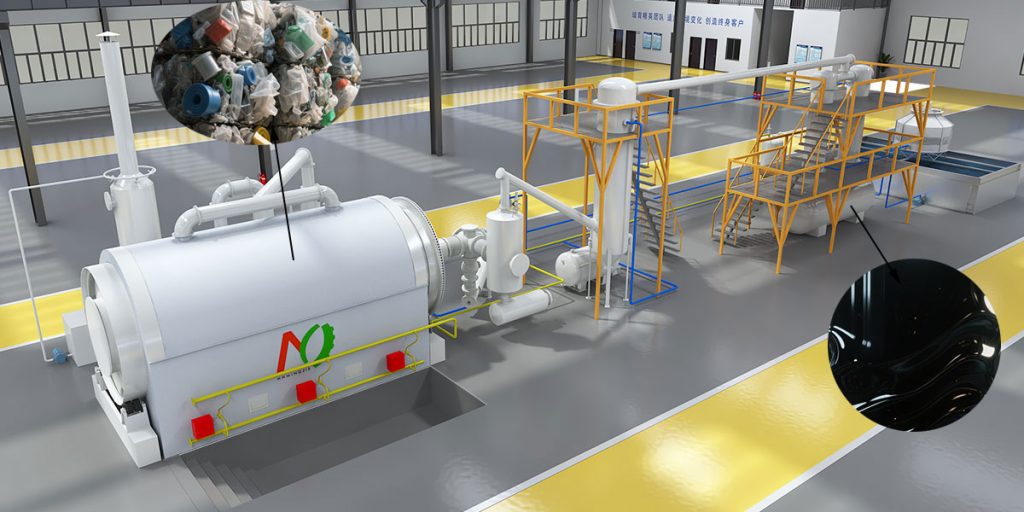
Application in Chemical Industry
The chemical industry is also inseparable from waste plastic to fuel pyrolysis plant. The gas and liquid products produced by the pyrolysis process contain a variety of organic compounds. After further processing and purification, these compounds can be used as chemical raw materials for the production of new plastic products, rubber products, coatings, solvents, etc. This not only realizes the recycling of plastics, but also reduces the demand for primary chemical raw materials such as petroleum.
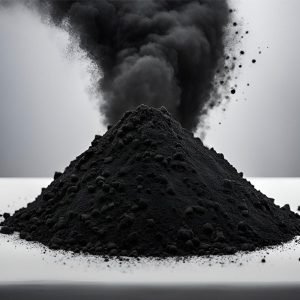
Environmental Protection Application
The application of waste plastic to fuel pyrolysis plant in environmental protection is of great significance. Traditional methods of waste plastic treatment, such as landfill and incineration, will cause serious pollution to soil, air and water sources. Pyrolysis technology treats waste plastic harmlessly, avoiding soil pollution and harmful gas emissions from incineration.
At the same time, the carbon black produced by plastic pyrolysis can be used as fillers and pigments for rubber products after treatment. This realizes the reuse of resources and reduces the generation of waste. The pressure of plastic waste on the environment is relieved from the source.
Conclusion
With the continuous advancement of pyrolysis technology, Mingjie plastic pyrolysis equipment is developing towards intelligence, high efficiency and low energy consumption. At present, we have small skid-mounted pyrolysis equipment, batch pyrolysis plant and continuous pyrolysis plant. In the future, Mingjie pyrolysis plants are expected to play a role in more fields and provide stronger support for the efficient recycling of resources and ecological environmental protection.