Pyrolysis equipment can obtain pyrolysis oil from plastic waste. In the pyrolysis process of waste plastics, pyrolysis oil is the core liquid product. It can be used as fuel oil or further refined into diesel or gasoline. Pyrolysis oil carries the dual transformation of environmental value and economic value of pyrolysis technology.
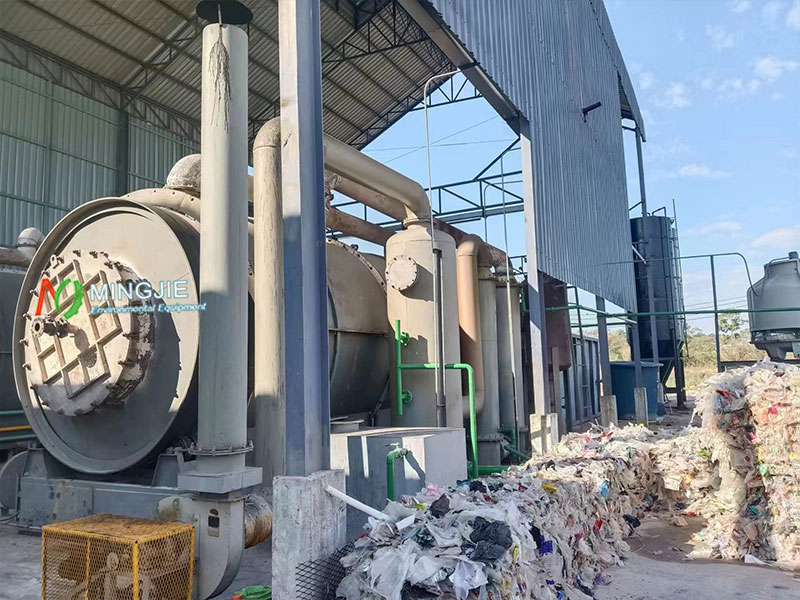
Composition of Pyrolysis Oil from Plastic Waste
The composition of pyrolysis oil generated by pyrolysis of waste plastics is complex, which mainly depends on the type of raw material and plastic pyrolysis process conditions.
Take common polyolefin plastics (polyethylene and polypropylene) as examples. The pyrolysis oil generated by pyrolysis of Polyethylene (PE) is mainly composed of alkanes and olefins. It has a high calorific value, usually up to 40 – 45 MJ/kg. It is similar to the calorific value of traditional diesel.
However, the pyrolysis oil produced by pyrolysis of polyvinyl chloride (PVC) plastics containing chlorine elements will contain corrosive substances such as hydrogen chloride. This not only affects the quality of oil products, but also causes corrosion to equipment.
In addition, the physical properties of pyrolysis oil, such as density, viscosity, and flash point, also vary due to different raw materials and processes. Generally speaking, its density is about 0.8 – 0.9 g/cm³, the viscosity changes significantly with temperature, and the fluidity is poor at low temperatures.
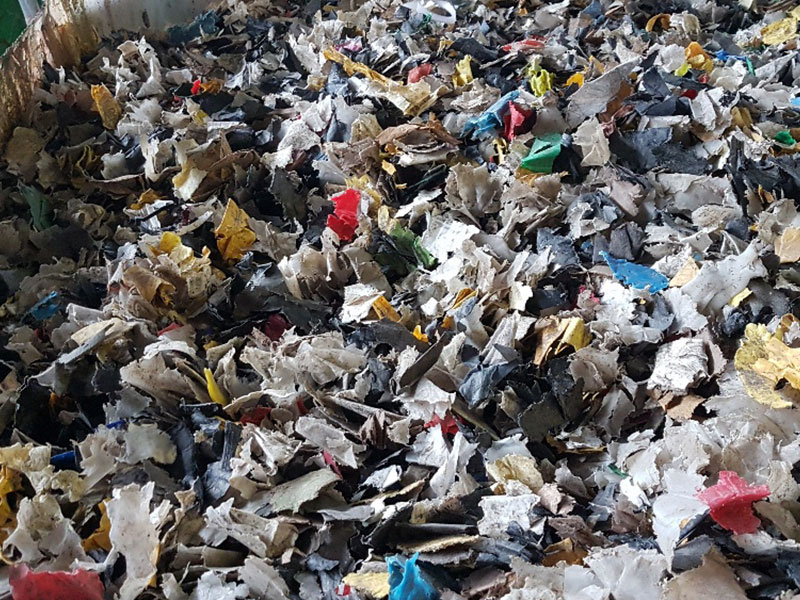
Application of Pyrolysis Oil from Waste Plastic
Pyrolysis oil currently shows its application value in energy and chemical industry.
In the energy field, after proper treatment, pyrolysis oil can be used as fuel for industrial boilers, kilns and other equipment. Pyrolysis oil from plastic waste can replace some fossil fuels and realize the recycling of energy.
In the chemical industry, olefins, aromatics and other components in pyrolysis oil are high-quality chemical raw materials. Pyrolysis oil from plastic waste can be further refined to produce high-value-added gasoline and diesel blending components. It can also be used as raw materials for the production of chemical products, such as plastics, rubber, and fibers.
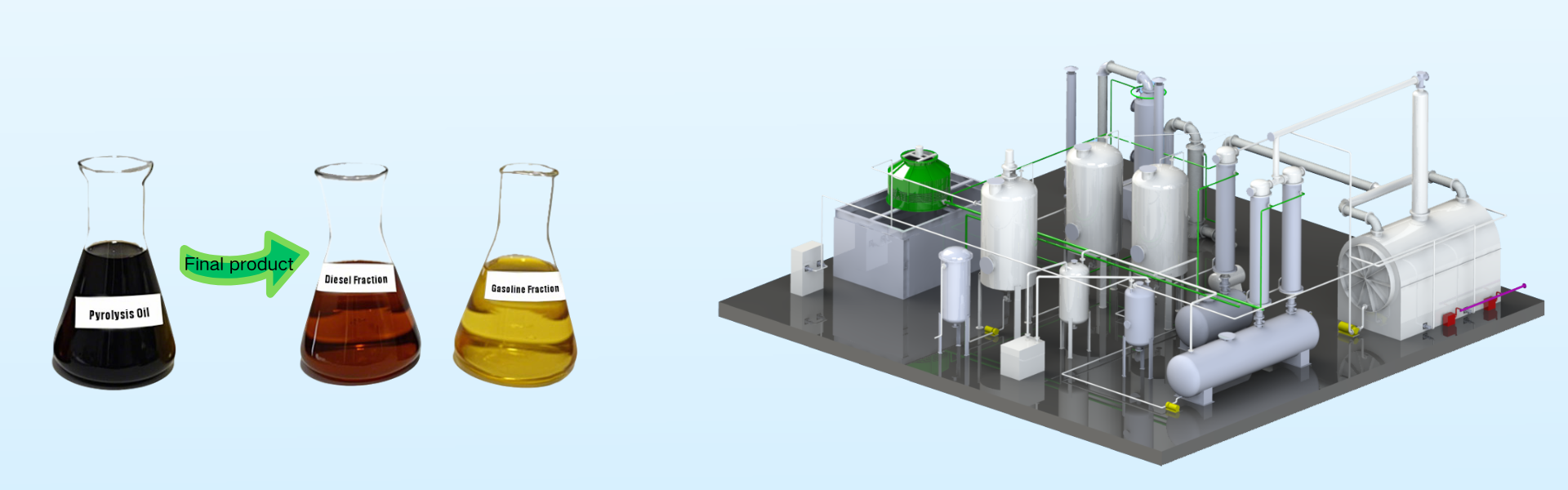
How to Improve the Quality of Pyrolysis Oil
In order to overcome the problems of complex composition and unstable quality of pyrolysis oil, Mingjie technicians have explored a variety of methods to improve its quality. Optimizing the pyrolysis process and refining Plastic Pyrolysis Oil To Diesel process are key means.
Plastic Pyrolysis Process
The pyrolysis process includes three key links: pretreatment, pyrolysis reaction, and product separation.
- Pretreatment stage. Waste plastics need to be sorted, cleaned, and crushed to remove impurities and improve pyrolysis efficiency.
- Pyrolysis reaction stage. The core principle of waste plastic pyrolysis is based on the thermal instability of polymers. Under the condition of oxygen isolation, the plastic molecular chain breaks under high temperature (300-600℃). Gradually degraded into small molecules, and finally formed gaseous, liquid and solid products.
- Product separation stage. Pyrolysis gas, pyrolysis oil and carbon black are separated and purified through condensation, fractionation and adsorption technologies.
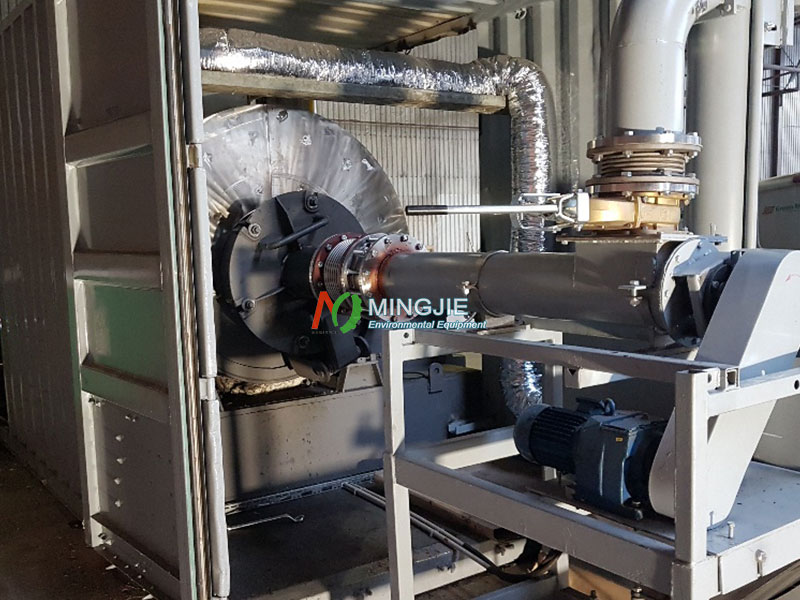
Optimizing the pyrolysis process enables the pyrolysis equipment to accurately control parameters, such as pyrolysis temperature, residence time and heating rate. This can make the plastic pyrolysis more complete, reduce the occurrence of side reactions, and thus improve the quality of pyrolysis oil.
Plastic Pyrolysis Oil To Diesel Process
Mingjie Group launched the pyrolysis oil distillation plant. It covert the pyrolysis oil to diesel through distillation and refining mechanisms. During the Plastic Pyrolysis Oil To Diesel process, the hydrocarbon molecular chains are destroyed and the molecules are reorganized to form new oil products. Subsequently, the oil is atomized into oil mist, which becomes liquid after condensation, and finally clear diesel is obtained.
The conversion of plastic pyrolysis oil into fuel oil (such as diesel, gasoline or heavy oil) requires processing through distillation equipment, thereby improving the quality and applicability of the oil.
Waste oil distillation equipment plays a vital role in the pyrolysis oil recovery and refining process. The distillation equipment has a high recovery rate, reaching 85-90%. It adopts full-process sealed operation, and the gas that cannot be condensed is discharged after exhaust gas treatment to meet the emission standards. The residual oil that cannot be distilled can be used as heavy diesel for combustion.