In recent years, mechanical recycling has become a prevalent mechanism for managing plastics. But chemical recycling technologies have greater availability for processing contaminated and complex mixed plastic streams. Due to the limitations of current mechanical recycling technologies, these heavily contaminated mixed plastic streams have not been recycled. Waste Plastic Recycling Pyrolysis is gaining attention as an alternative to mechanical recycling and incineration due to its wider range of treatment options.
Plastic recycling pyrolysis technology brings new hope to solve the problem of plastic pollution and realizes the recycling of mixed plastics. As a chemical recycling method, it can decompose plastics into small molecules by high temperature in an oxygen-free or low-oxygen environment.
The complex composition of plastics is a major technical challenge faced by pyrolysis technology. Various types of plastics are collected in the recycling of waste plastics, including polyethylene (PE), polypropylene (PP), polyvinyl chloride (PVC), polystyrene (PS), etc. The chemical structures and pyrolysis characteristics of these plastics are different, making the pyrolysis process difficult to control.
Polyolefin plastics mainly produce hydrocarbon compounds during pyrolysis. During the pyrolysis process, polyvinyl chloride releases corrosive gases such as hydrogen chloride. It not only corrodes the equipment, but also affects the quality of the pyrolysis products. If the waste plastics contain other impurities, such as rubber, fiber, and metal, the complexity of pyrolysis will be further increased.
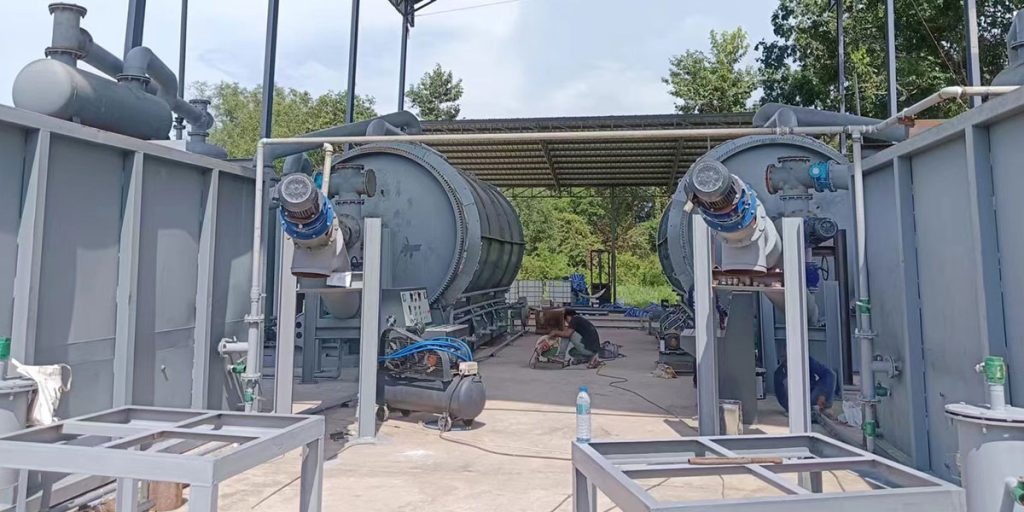
Pyrolysis plant use pyrolysis technology to heat mixed plastics under oxygen-free conditions. Ultimately, waste plastics are converted into pyrolysis oil, syngas and carbon black. The resulting oil-gas mixture is transferred to a condenser and cooled into pyrolysis oil. This fuel oil can be further refined into diesel or gasoline base oil through distillation unit.
Application of Plastic Pyrolysis Technology
Plastic recycling pyrolysis technology is moving from the laboratory to a critical stage of industrial large-scale application.
The application of plastic recycling pyrolysis plant is gradually emerging around the world. According to a report by Market Research Future (MRFR), the global plastic processing capacity of pyrolysis plant is expected to increase from 4.1 million tons in 2022 to 12 million tons in 2030. This growth trend reflects the increasing importance of pyrolysis pyrolysis technology in the global plastic recycling field. More and more companies and countries are beginning to pay attention to and adopt pyrolysis technology to solve the plastic waste problem.
Global Plastic Pyrolysis Plant
In terms of regional distribution, different regions have different application and development priorities for plastic recycling pyrolysis technology.
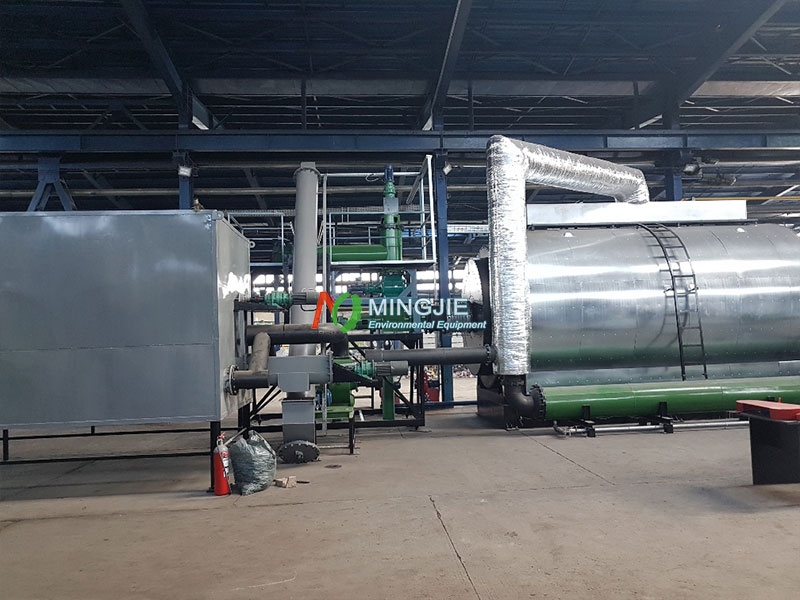
Due to its strong environmental awareness and strict relevant policies and regulations, Europe is in a leading position in the research and development and application of plastic pyrolysis technology. Many European countries actively promote the construction of pyrolysis projects and regard it as an important means to achieve a plastic circular economy.
For example, some companies in Germany, the Netherlands and other countries have established large-scale plastic pyrolysis plants. They process various types of waste plastics to produce high-quality oil products and chemical raw materials, realizing the high-value utilization of waste plastics.
North America, especially the United States, has invested a lot of resources in the research and innovation of pyrolysis technology. Some universities and research institutions cooperate with enterprises to continuously improve the efficiency and product quality of plasic recycling pyrolysis technology.
At the same time, some large companies in the United States have also begun to get involved in the field of plastic pyrolysis. They invest in the construction of pyrolysis equipment to meet the growing demand for plastic waste treatment.
The Asia-Pacific region is the world’s largest plastic production and consumption region. Although the application of pyrolysis technology started relatively late, it has great development potential.
In recent years, countries in the Asia-Pacific region have increased their investment in plastic recycling and pyrolysis technology. They have introduced relevant policies to encourage companies to use pyrolysis technology to treat waste plastics. For example, China has promoted the construction of a number of pyrolysis projects through policy guidance and financial support. This has improved the application level and industrial scale of plastic recycling pyrolysis technology. India is also actively exploring plastic pyrolysis technology and business models suitable for its national conditions, and gradually increasing the recycling rate of plastic waste.
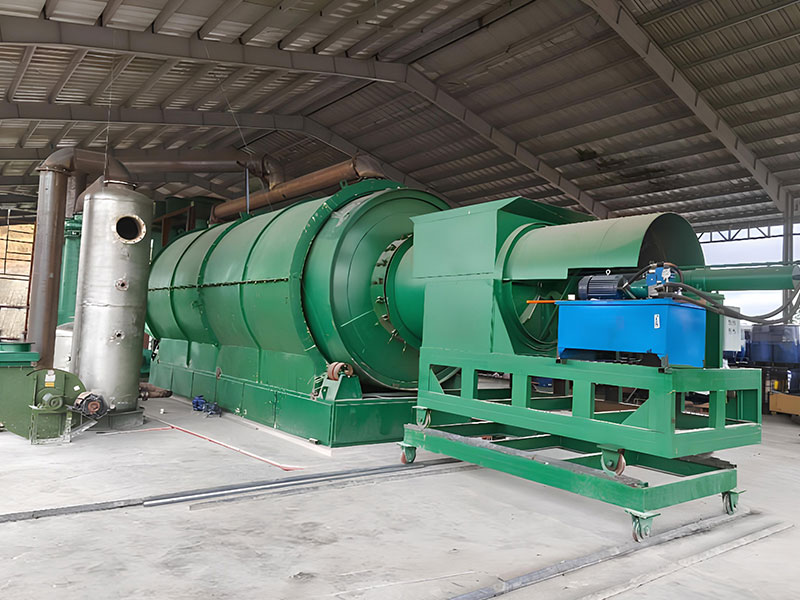
Optimization of Pyrolysis Plant
As the core equipment of plastic pyrolysis, the rationality of its design directly affects the pyrolysis performance and production efficiency. With the deepening of the understanding of the pyrolysis process, the reactor design is constantly optimized, showing a trend of being more complex and efficient.
Traditional pyrolysis reactors are mostly simple batch reactors. In order to further improve the pyrolysis efficiency and product quality, continuous pyrolysis reactors are optimized and designed. Compared with the traditional batch pyrolysis process, the continuous pyrolysis plant can achieve a continuous and stable supply of waste plastics. It avoids downtime caused by batch operation and improves production efficiency and waste plastic processing capacity.
The application of pyrolysis technology will promote the plastic recycling industry to develop in the direction of intelligence and automation. As pyrolysis technology continues to mature, the application of intelligent monitoring and automatic control technology in the pyrolysis process will become more and more extensive. Through intelligent equipment and systems, precise control and optimized management of the pyrolysis process can be achieved.
Fully Automatic Pyrolysis Plant
The fully automatic pyrolysis plant adopts continuous feeding system, intelligent monitoring, automatic control and other technologies. The continuous feeding system can achieve a continuous and stable supply of waste plastics.
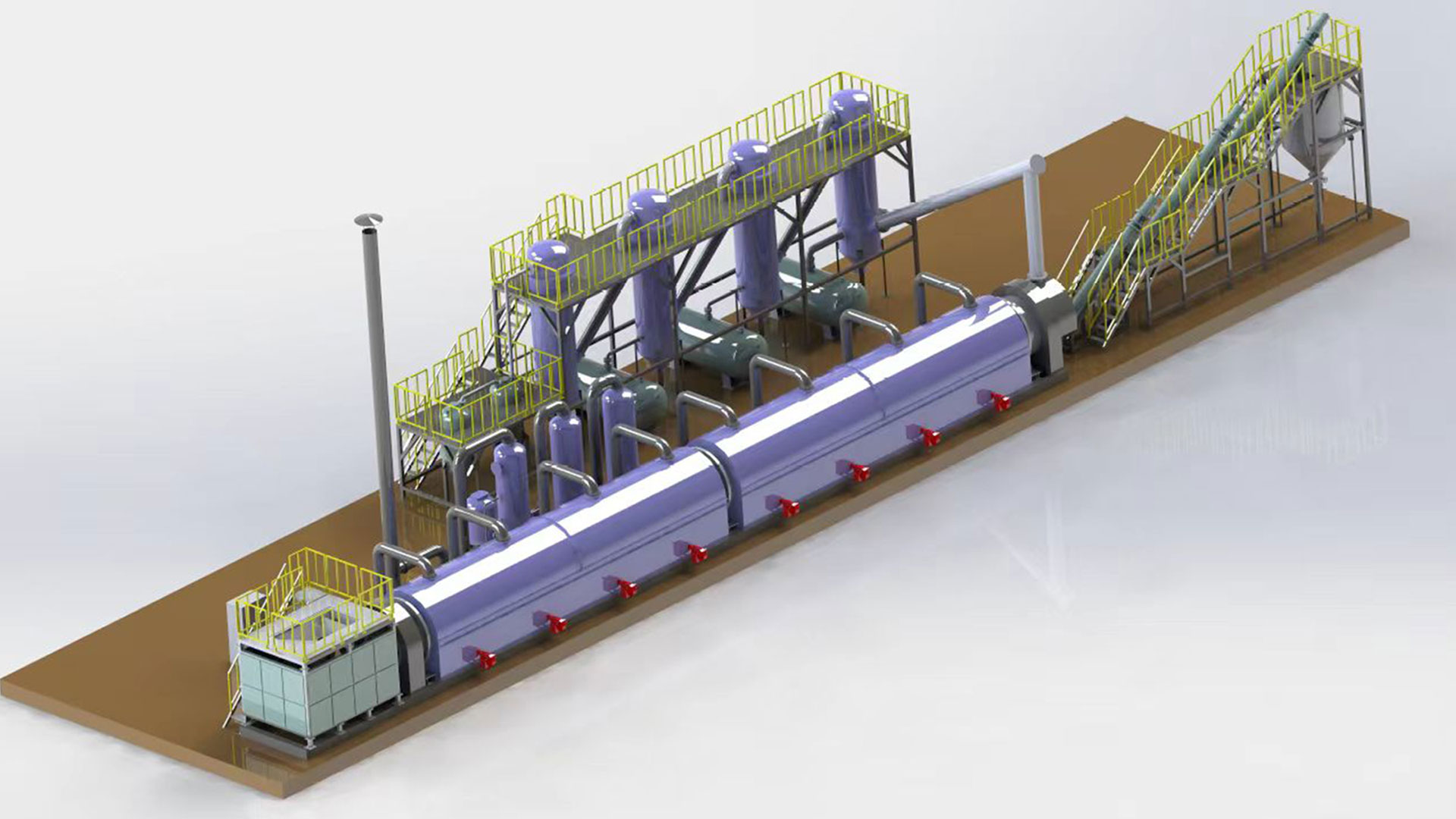
The intelligent monitoring system installs various sensors in the pyrolysis equipment, such as temperature sensors, pressure sensors, etc. It can collect various parameters in the pyrolysis process in real time and transmit these data to the control system.
The automatic control technology realizes the automatic operation and optimization control of the pyrolysis process. Through the automatic control system, various parameters of the pyrolysis equipment, such as heating temperature, feeding speed, gas flow, etc., can be automatically adjusted according to the preset program.
The combination of intelligent monitoring and automated control technologies further improves the safety and stability of the plastic pyrolysis process. They can promptly detect and solve problems that arise during the pyrolysis process, reducing equipment failures and accidents. At the same time, they can also optimize the pyrolysis process and improve production efficiency and product quality.
Solution of Waste Plastic Recycling Pyrolysis
While plastic pyrolysis technology solves the problem of plastic pollution, it also faces some environmental challenges of its own. The pyrolysis process is energy-intensive and requires a lot of heat to decompose the plastic, which usually needs to be generated by an external source.
Taking the common continuous pyrolysis furnace as an example, the pyrolysis temperature of 400-600°C is required to pyrolyze plastic. For every ton of waste plastic processed, it may take 100-150 kg of standard coal. This not only increases energy consumption, but also raises questions about the overall carbon footprint of the technology.
Pyrolysis byproducts, such as gases and residues, can also cause harm if not managed properly. The pyrolysis process of waste plastics releases volatile organic compounds (VOCs) and other pollutants. These substances pose health risks to humans and animals.
In response to these environmental issues, Mingjie Pyrolysis Plant began to explore the use of renewable energy, such as syngas, to provide heat for the pyrolysis process. This can significantly reduce the carbon footprint and improve the sustainability of pyrolysis technology.
In terms of plastic pyrolysis product treatment, we use more efficient waste gas treatment equipment and residue recovery equipment.