Plastic pyrolysis chemical recycling is an advanced technology that converts waste plastics into pyrolysis oil, syngas, and carbon black through high-temperature anaerobic decomposition. It specializes in waste plastics that cannot be processed by mechanical recycling: such as mixed films and composite packaging (PE/PP/PS accounts for 70%). Pyrolysis chemical recycling complements the mechanical recycling of PET bottles.
Plastic pyrolysis chemical recycling technology can be mainly divided into thermal cracking, catalytic pyrolysis and thermal cracking-catalytic modification.
Thermal cracking is the most basic plastic pyrolysis method. It simply relies on providing heat energy to overcome the activation energy required for plastic polymer cracking.
Catalytic pyrolysis is to add a catalyst during the plastic pyrolysis process to reduce the activation energy required for the reaction. Commonly used catalysts include solid acid catalysts such as solid aluminum silicate and molecular sieves. They can provide proton hydrogen during the reaction, so that the reaction is accompanied by a hydrogen transfer process, thereby having an isomerization function.
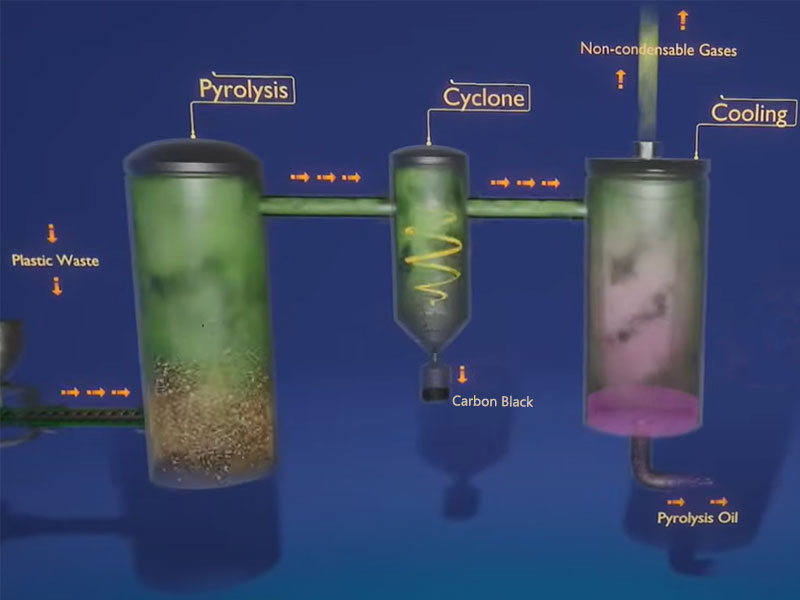
Thermal cracking-catalytic modification combines the advantages of thermal cracking and catalytic pyrolysis. First, the waste plastic is pyrolyzed at high temperature to produce high-temperature pyrolysis gas. Then the pyrolysis gas is subjected to the action of a catalyst to obtain a high-quality oil product. This method is mostly used to treat mixed waste plastics and is flexible to operate.
Pyrolysis Chemical Recycling Process
The process of plastic pyrolysis chemical recycling usually includes three main steps: pretreatment, pyrolysis reaction and product treatment.
Pretreatment
The pretreatment link is crucial. Its purpose is to remove impurities and moisture in waste plastics, thereby improving the efficiency of pyrolysis reaction and product quality.
At this stage, the collected waste plastics will first be sorted. Because the pyrolysis characteristics and products of different plastics are different, classification treatment helps to improve the purity and value of subsequent pyrolysis products. For example, common plastics such as polyethylene (PE), polypropylene (PP), and polystyrene (PS) are classified separately.
Then, physical methods (screening, air separation) are used to remove solid impurities such as stones, metals, and sawdust from waste plastics. Dirt and grease on the surface are removed by water washing or solvent washing. Then use drying methods to remove moisture to prevent moisture from affecting the reaction during the pyrolysis process.
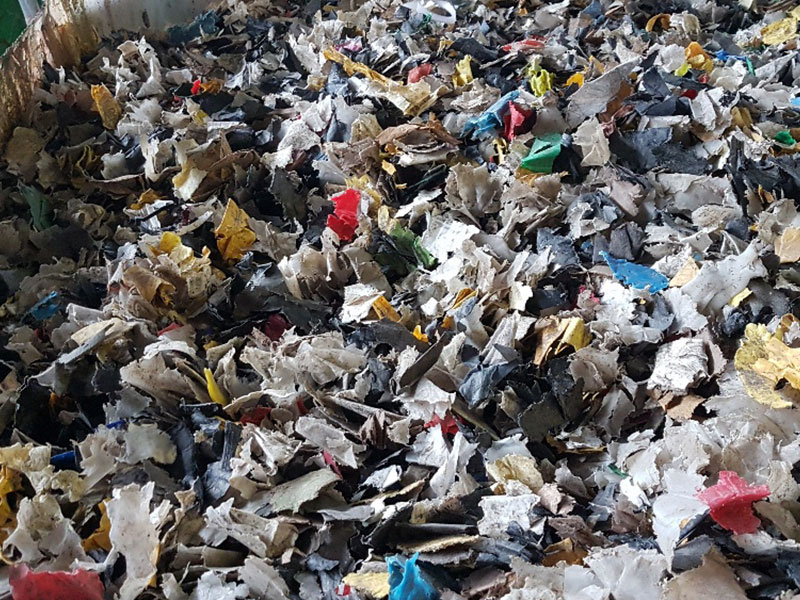
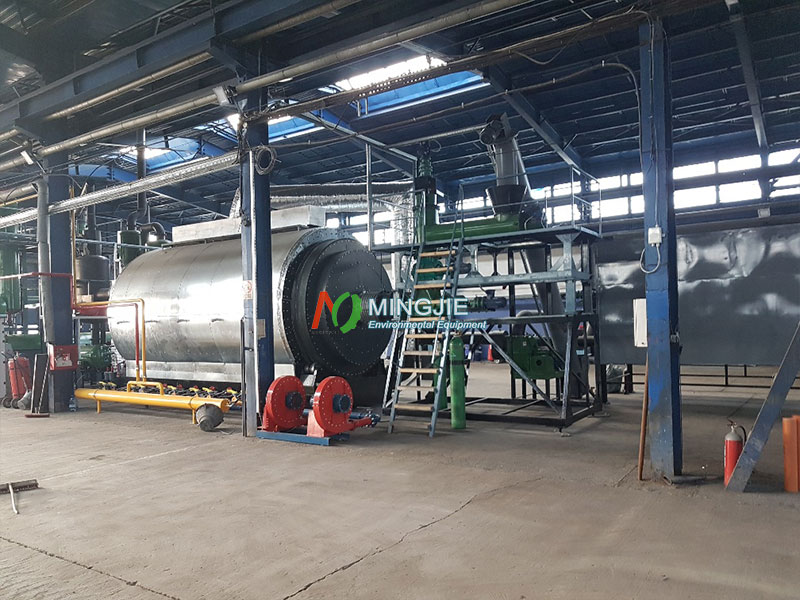
Plastic Waste Pyrolysis Process
After pretreatment, waste plastics enter the pyrolysis reaction stage. This Plastic Waste Pyrolysis Process stage is the core link of plastic pyrolysis chemical recycling. The pretreated waste plastics are sent to the pyrolysis reactor and heated under high temperature conditions (between 400°C and 600°C).
In the pyrolysis furnace, as the temperature rises, the chemical bonds in the plastic molecules gradually break, cracking reactions occur, and macromolecular polymers decompose into small molecular compounds. The pyrolysis products mainly include liquid oil, gaseous products and solid residues.
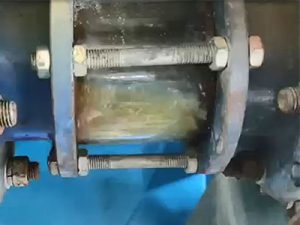
Pyrolysis Product Treatment
After the pyrolysis reaction is completed, the product needs to be treated. The purpose of pyrolysis product treatment is to separate and purify the gas, liquid and solid products obtained from the pyrolysis reaction.
Liquid products are separated from gas and liquid through a condensation device. The difference in boiling points of different substances is used to cool gaseous hydrocarbon substances into liquids. Liquid products are further separated and purified through distillation, filtration and other technologies. Oil products of different fractions are obtained, such as gasoline fractions and diesel fractions.
The gaseous products pass through a gas purification device to remove impurities, such as hydrogen sulfide and carbon dioxide. Then, they are used for power generation, industrial fuel or chemical raw materials as needed.
For the solid product carbon black, it undergoes further treatment, such as crushing and purification.
In Summary
With the continuous maturity of pyrolysis technology and the gradual reduction of the cost of pyrolysis equipment, the plastic pyrolysis chemical recycling industry will usher in a golden period of rapid development. In the future, more pyrolysis chemical recycling plants will be built and put into production, forming a large-scale and industrialized development pattern.
These plastic recycling plants use advanced pyrolysis processes and equipment, such as continuous pyrolysis processes and intelligent pyrolysis equipment. They realize the continuous and automated processing of waste plastics, reduce costs and improve production efficiency.