Biochar refers to a carbon-rich solid material formed by pyrolysis of biomass (such as agricultural and forestry waste, animal feces) at high temperature (300-700℃) in an oxygen-free or low-oxygen environment. The biochar making machine is a key link in converting large scale waste biomass into high-value-added charcoal products.
Unlike ordinary charcoal, the production of biochar focuses more on the renewability of raw materials and the stability of products. Its carbon content is usually more than 60%, and it has a highly aromatic chemical structure. This makes biochar difficult to decompose in the natural environment. It can seal carbon elements for a long time and become an important tool for coping with climate change.
The raw materials for biochar making are extremely diverse. Straw, rice husks, nut shells, sawdust, and branches can all be used as raw materials for producing biochar. These waste biomass are converted into biochar through pyrolysis carbonization plants, realizing the pyrolysis waste to energy.
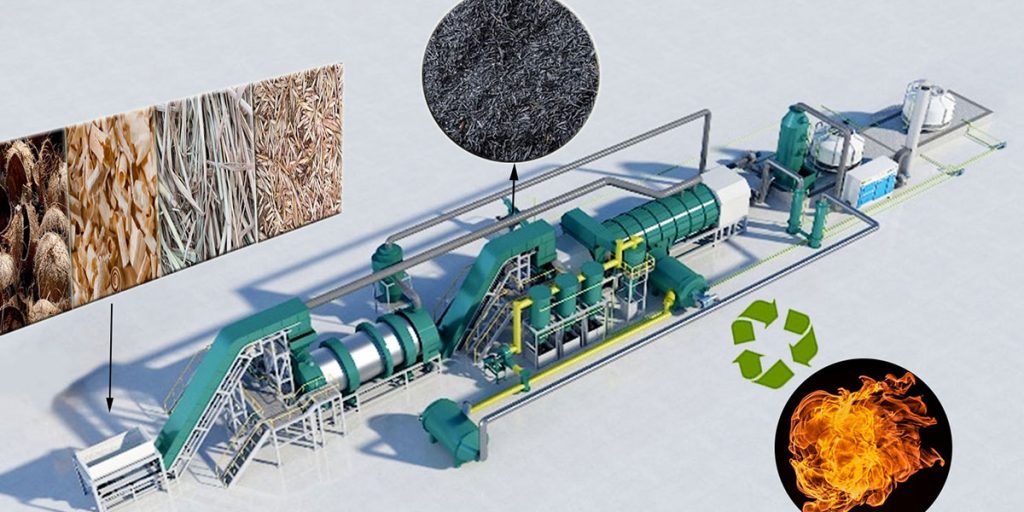
Biochar Making Process
From the screening and pretreatment of raw materials to the precise control of the pyrolysis process, and then to the quality inspection of the finished product, each step directly affects the performance and application of biochar. A deep understanding of the production chain of biochar can not only optimize production efficiency, but also lay the foundation for its large-scale application.
Raw Material Selection
The selection of raw materials for biochar production is extremely flexible. However, the characteristics of the raw materials directly determine the quality of the final product.
Agricultural waste is the most common source of raw materials, including straw, rice husks, sugarcane bagasse, etc. This type of raw material has a large output, wide distribution, and is rich in cellulose and lignin. Agricultural waste can form a stable carbon structure after pyrolysis.
Forestry waste wood chips, branches, and coconut shells are ideal raw materials for high-value-added biochar making. Due to the high lignin content, the biochar has more developed pores and better adsorption performance.
In addition, livestock and poultry manure and sludge can also be used as raw materials to realize the resource utilization of waste. But it is necessary to remove impurities and harmful substances.
Pretreatment
Raw material pretreatment is an important step to improve production efficiency and product quality.
The first is crushing and screening, crushing the raw materials to a suitable particle size (5-20 mm), increasing the heating area, and ensuring uniform pyrolysis reaction.
The second is drying treatment, reducing the moisture content of the raw materials to 10%-20% to reduce energy consumption during pyrolysis. Excessive moisture will make it difficult to increase the pyrolysis temperature, and will also increase the moisture content in the bio-oil, affecting the quality of by-products. For high-moisture raw materials such as livestock and poultry manure, the moisture content can be reduced by natural drying or mechanical drying.

Continuous Pyrolysis Process
Continuous Pyrolysis is the core link of biochar making. Biomass undergoes a series of chemical reactions such as decomposition and condensation through high temperature heating in an oxygen-free or low-oxygen environment. Ultimately, the biochar making equipment produces solid biochar, liquid bio-oil and syngas.
Mingjie pyrolysis reactor adopts double-layer insulation function, which is suitable for large-scale biochar making and can process 100kg-5000kg of biomass per hour. The biomass carbonization plant has strict requirements on the particle size of raw materials, requiring the size to be less than 20mm, and less than 15%.
Biomass Pyrolysis Product Collection
After the pyrolysis reaction is completed, the products need to be separated and collected. Solid biochar is discharged through a water-cooled spiral device and can be directly collected into a packaging bag.
The recovery of liquid and gas products can not only improve resource utilization, but also provide energy for the production process. Bio-oil can be collected through a condensation system and used as fuel or chemical raw materials after refining. Syngas can be directly burned to provide heat for the pyrolysis reaction and achieve energy self-sufficiency.
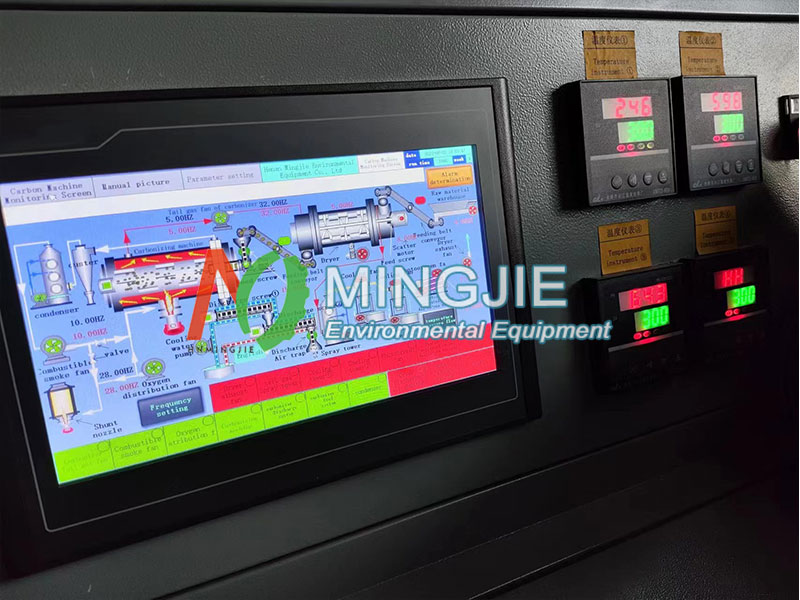
Environmental Protection and Safety Control
A small amount of volatile organic compounds (VOCs) and tar will be produced during the biochar making process. They are purified by the waste gas treatment system (such as activated carbon adsorption and catalytic combustion) and then discharged to avoid air pollution.
Production wastewater (equipment cooling water) is recycled after precipitation, filtration and other treatments, achieving zero emissions.
Safety management is an important guarantee for large-scale biochar production. The pyrolysis reactor is strictly sealed to prevent oxygen leakage from causing combustion or explosion. The biochar production equipment is equipped with a PLC intelligent control system. If the equipment is abnormal, the alarm device will be triggered.
Operators need to take protective measures to avoid contact with high-temperature pyrolysis equipment and harmful gases. The raw material storage area should be away from fire sources to prevent flammable biomass from spontaneous combustion.
Large Scale Biochar Production
Standardized production is the premise of large-scale biochar making. The performance of biochar produced by different raw materials and processes varies greatly, and a unified quality standard needs to be established. In addition, a complete production process specification needs to be formulated to ensure the stability of product quality.
Biochar production is moving towards “green, intelligent, and customized”. Through raw material pretreatment, process parameter optimization and technological innovation, the biochar production cost will be further reduced, and the performance will be more accurately controllable.