Pyrolysis technology is one of the most environmentally friendly and cost-effective methods for the treatment of waste tyres. It can process recyclables and obtain valuable products from waste. The tyre pyrolysis process is a thermal decomposition process. Pyrolysis plants convert waste tyres into liquid oil (pyrolysis oil), solid residues (carbon black), steel wire and synthesis gas at high temperature and in an oxygen-free environment.
The rubber in tire is composed of long-chain polymers. These polymers are connected to each other by covalent bonds, forming a complex and stable molecular structure. During the rubber pyrolysis process, the heat energy gives the molecules enough energy to cause these covalent bonds to begin to break.
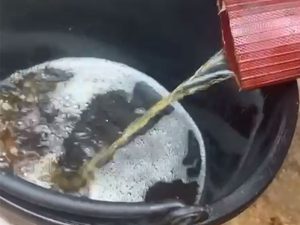
These molecular fragments further undergo complex chemical reactions such as rearrangement, cyclization, and dehydrogenation, thereby converting into various low-molecular compounds. Some molecular fragments will be converted into hydrocarbon compounds containing carbon and hydrogen elements. These hydrocarbon compounds exist in gaseous form during the pyrolysis process. When the temperature drops, they will condense into liquid fuel oil. The composition of tyre pyrolysis oil is similar to that of petroleum products, mainly containing alkanes, olefins, aromatics, etc.
A large amount of carbon black is originally added to the tire as a reinforcing agent to improve the strength and wear resistance of the tire. During the tyre pyrolysis process, these carbon blacks basically remain in a solid state and will not undergo obvious chemical changes. They are just separated from other decomposition products. At the same time, some incompletely decomposed organic matter will remain during the tire pyrolysis process to form pyrolytic carbon black.
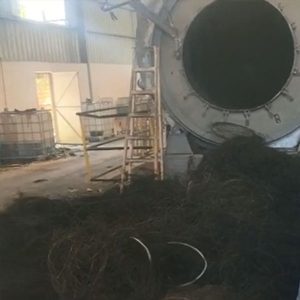
This pyrolytic carbon black has certain differences from the original carbon black in microstructure and surface properties. But it still has a high specific surface area and adsorption performance. It can be further processed and modified and re-applied to industries, such as rubber, plastics, and inks.
The steel wire in the tire does not participate in the chemical reaction during the tyre pyrolysis process. Due to its good thermal stability, it remains solid at high temperatures. When the pyrolysis reaction is over, the steel wire can be efficiently separated from the pyrolysis product by physical separation methods, such as magnetic separation. These recycled steel wires can be directly returned to the furnace for smelting and reused in steel production.
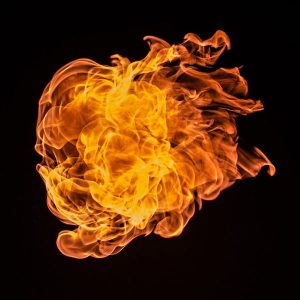
During the tyre pyrolysis process, some combustible gases are also produced. The main components include small molecular hydrocarbons, such as hydrogen (H₂), methane (CH₄), and ethane (C₂H₆). These combustible gases are produced because some carbon-hydrogen bonds (C-H) break during the cracking of polymers, releasing hydrogen atoms. Hydrogen atoms combine with other small molecules produced by cracking to form these combustible gases.
These synthetic gases have high calorific values. For example, the calorific value of hydrogen is as high as 142.35kJ/g, and the calorific value of methane is about 55.5kJ/g. They can serve as a supplementary energy source for the pyrolysis process, providing continuous heat for the pyrolysis reaction and achieving energy self-sufficiency.
Factors Affect Tyre Pyrolysis Process
The main factors affecting the tyre pyrolysis process include temperature, pyrolysis equipment and material size.
Temperature
Temperature is one of the most critical factors in the tyre pyrolysis process. It plays a decisive role in the rate and product distribution of the pyrolysis reaction. Generally speaking, as the pyrolysis temperature increases, the thermal motion of molecules intensifies and the reactant molecules gain more energy. As a result, the collision frequency and effective collision probability between molecules increase, which greatly accelerates the rate of the pyrolysis reaction.
In terms of product distribution, there are significant differences in the composition and properties of pyrolysis products at different temperatures.
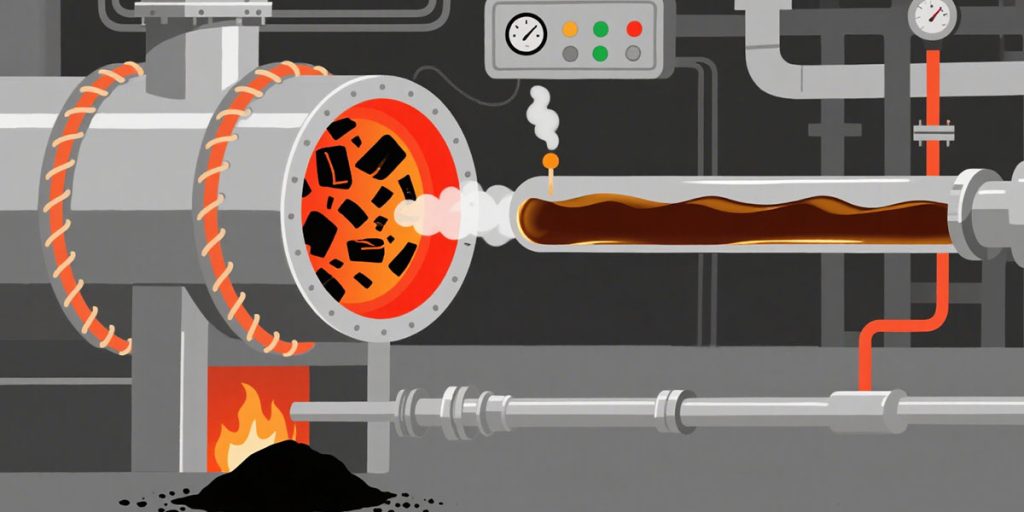
When the pyrolysis temperature is in a relatively low range, such as 400℃ – 500℃, the content of fuel oil and carbon black in the pyrolysis products is relatively high. This is because within this temperature range, the high molecular polymers in the tire mainly undergo preliminary cracking reactions, and the macromolecular chains break to form relatively small molecular fragments. Part of these molecular fragments combine to form fuel oil, and the other part is converted into carbon black.
As the temperature further increases, above 500℃, the yield of light hydrocarbon gas will increase significantly. This is because at high temperatures, products such as fuel oil and carbon black will undergo secondary cracking reactions. This leads to a significant increase in the production of light hydrocarbon gases, while the yields of fuel oil and carbon black decrease accordingly. If the temperature is too high, it may also lead to the cracking of products such as tar, affecting the quality and subsequent application of the tyre pyrolysis products.
During the tyre pyrolysis process, the heating rate needs to be accurately controlled to avoid heating too fast or too slow. If the heating rate is too fast, it may cause local overheating. This makes it difficult for the pyrolysis reaction to proceed evenly, thus affecting the quality and yield of the product.
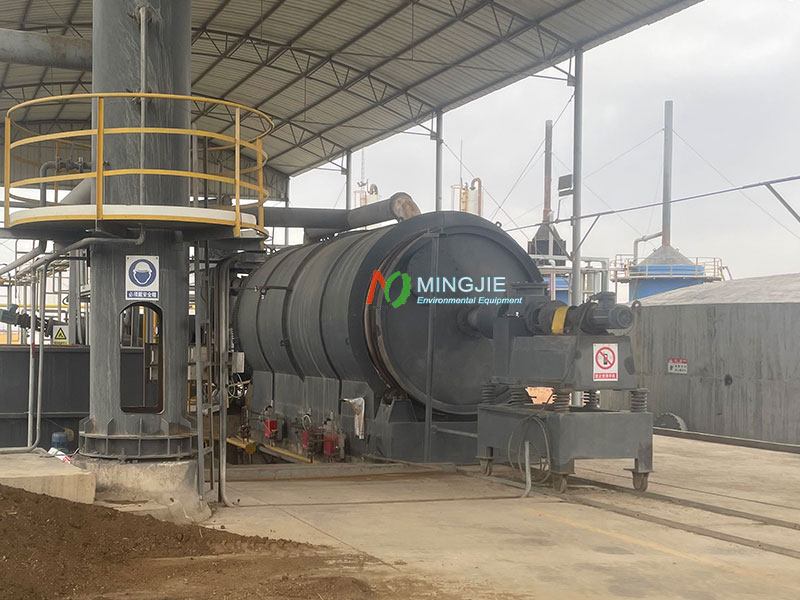
Tyre Pyrolysis Reactor
The type and configuration of the pyrolysis reactor also affect the products of waste tyre pyrolysis process. There are several main types of tyre pyrolysis reactors.
Fixed bed reactors are very simple to design and operate, especially in the laboratory. However, due to the low heat transfer rate of this pyrolysis reactor, it is difficult to operate continuously and scale up.
Fluidized bed reactors can increase oil production and support continuous operation. However, the design and operation of the system are complex, and the operation of the reactor requires high investment, which limits the utilization of fluidized bed reactors.
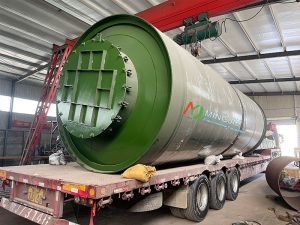
The rotary kiln reactor has attracted much attention due to its simple design and construction. It is a rotating cylindrical reaction vessel. The tires are constantly rolling in the pyrolysis reactor as the kiln body rotates. Fully contacting the heat source, and the pyrolysis reaction is carried out in the pyrolysis reactor. The rotary kiln reactor has the advantages of large processing capacity, good pyrolysis effect, and high product quality.
The microwave reactor has the advantages of fast heating speed, uniform heating, energy saving and high efficiency. However, there are still some challenges in the large-scale industrial application of microwave pyrolysis technology, such as the high cost of microwave equipment and the uniformity of microwave power.
Rubber Particle Size
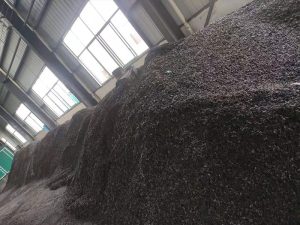
The size of the rubber particles also has an important influence on the tyre pyrolysis process. The smaller the particle size, the larger the specific surface area. It can increase the contact area with the pyrolysis medium, making the heat and mass transfer process faster and more complete. This is conducive to the waste tyre pyrolysis process and improves the reaction rate.
Studies have shown that when the tire particle size is reduced from 2mm to 0.1mm, the pyrolysis oil yield increases by 12.9%. Smaller particle size rubber particles can also make the pyrolysis reaction more uniform and reduce local overheating or incomplete reaction.
When the particle size of the rubber particles is too large, the internal heat and mass transfer are restricted, resulting in uneven pyrolysis reaction. This may result in incomplete pyrolysis of some rubber particles, reducing pyrolysis efficiency and product quality.
Pyrolysis Plant Manufacturer
As an innovative solution to the problem of waste tires, tire pyrolysis technology has shown irreplaceable importance in the fields of environmental protection and resource utilization. Mingjie Group is a professional pyrolysis plant manufacturer. Engineers have continuously optimized the pyrolysis plant, and the continuous pyrolysis equipment has achieved intelligent, continuous and large-scale applications.
The intelligent system can realize real-time monitoring and precise control of the pyrolysis process, improve production efficiency and the stability of product quality. The continuous tire pyrolysis plant can reduce the intermittent time in the production process, improve production efficiency and reduce production costs. Fully automatic tyre pyrolysis plant can achieve large-scale production, further reduce the production cost of unit products, and improve economic benefits.