Pyrolysis of mixed plastic waste is a promising chemical recycling method, it can convert plastic waste into pyrolysis oil. Pyrolysis oil can be further processed to produce chemicals or fuels. Plastic pyrolysis oil can also be used as a chemical feedstock to make new plastic products, thus achieving closed-loop recycling.
Pyrolysis technology enables the recycling of plastic waste without reducing the quality of the product. This is different from mechanical processes, where the quality of recycled plastic deteriorates after multiple processing.
Pyrolysis of mixed plastic waste has been successfully used as an environmentally friendly alternative to treat plastic waste that cannot be processed by mechanical recycling and supports a more circular economy. Pyrolysis is a thermochemical conversion process that takes place at temperatures between 400 and 600°C in the absence of oxygen. The products of the chemical reactions that occur during pyrolysis are gases, fuel oil and solid carbon black.
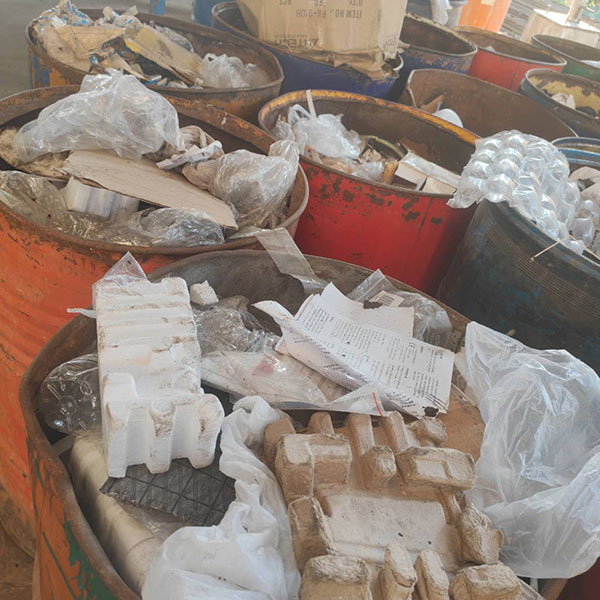
Challenges of Mixed Plastic Waste Pyrolysis
Complexity of Mixed Plastic Compositions
One of the main challenges in pyrolysis of mixed plastic waste is the complexity of its composition. Mixed plastics from urban waste are heterogeneous and often contain mixed polyethylene, polypropylene and polystyrene (PE/PP/PS) as well as multilayer packaging and fiber-reinforced composites. In fact, mixed plastics are difficult to separate and pyrolysis is more complicated than high-purity single plastics.
The high Cl content in PVC (56%) is one of the main issues in the pyrolysis of mixed plastic waste. This is because chlorinated compounds are formed, which are harmful from the perspective of corrosion and environmental impact. In addition, the chlorine content in the pyrolysis oil/wax products is high, requiring additional post-treatment before they can be used as petrochemical feedstocks.
Pyrolysis of PET (polyethylene terephthalate) is technically feasible, but there are significant defects in practical applications. PET decomposition produces acidic substances, such as acetic acid and phenols, which corrode equipment pipelines. Polycyclic aromatic hydrocarbons (PAHs) and oxygen-containing organic matter (such as acetaldehyde) are environmentally toxic and increase the cost of exhaust gas treatment.
PET Pyrolysis oil is difficult to be used directly as fuel due to its high oxygen content (15-20%) and poor stability. It needs to be hydrogenated and deoxygenated to improve its quality, which significantly increases the cost. PET has high melt viscosity at high temperatures and is easy to clog the reactor, requiring the addition of fluidizing medium or pre-crushing.
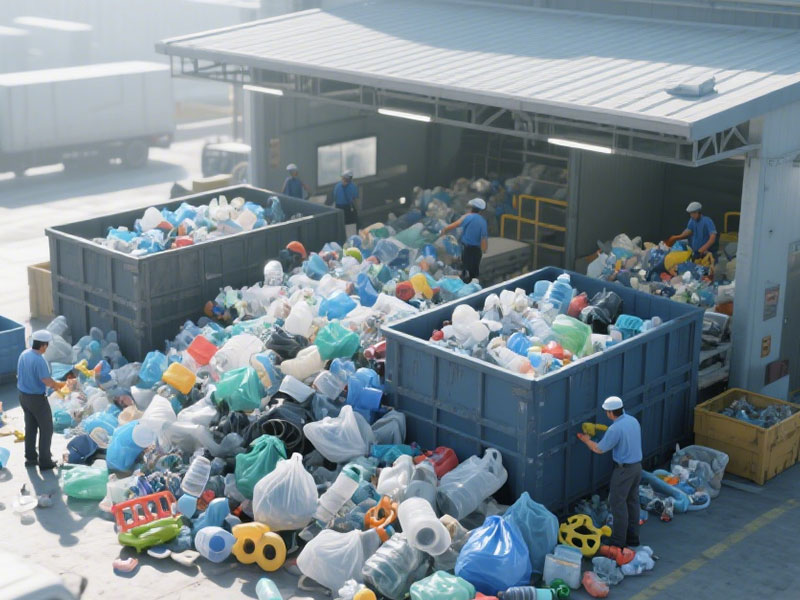
Contaminants and Additives
Another aspect in the pyrolysis of mixed plastic waste is the presence of contaminants and additives in the feed.
For example, organic contaminants, paper and cardboard derived contaminants may be present in plastic waste. These contaminants come from labels, bottle caps, lids, food residues and introduce unwanted elements in the feed. The presence of these elements can cause operational problems during the pyrolysis process.
Almost all plastic products contain additives to enhance the polymer properties and extend its service life. Typically, plastic waste is washed using cold or hot water with the aid of detergents and/or caustics.
How to Achieve Efficient Pyrolysis of Mixed Plastic Waste
Pretreatment of Mixed Plastic
The pretreatment stage is the basis of the entire pyrolysis of mixed plastic waste process. Its purpose is to remove impurities in mixed plastic waste, improve the purity of pyrolysis raw materials, and create conditions for the smooth progress of subsequent pyrolysis reactions.
Mixed plastic classification is a very challenging task. Due to the wide range of sources and types of mixed plastic waste, a variety of technical means are required for accurate identification and classification. The cleaning process is crucial, which can remove impurities such as oil, dust, and dirt attached to the surface of the plastic.
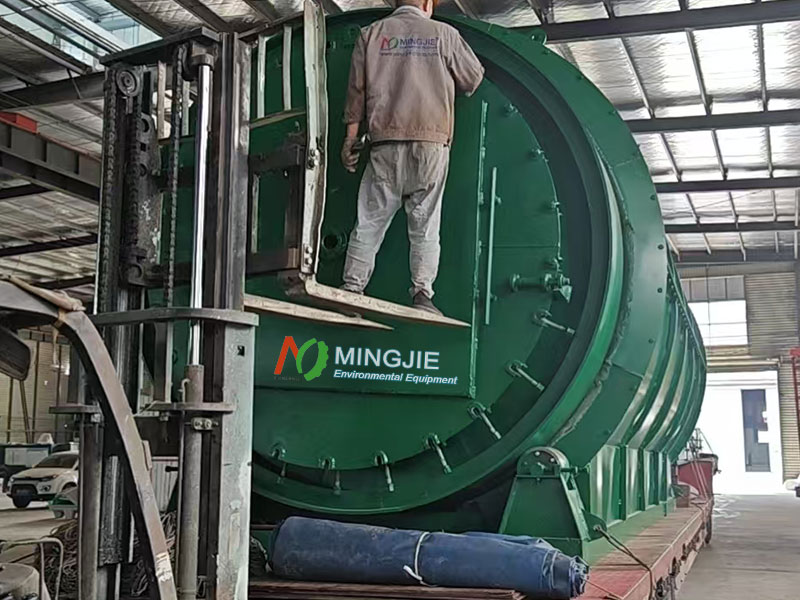
Crushing is the last step of pretreatment in a continuous pyrolysis plant. The plastic waste is crushed into suitable sizes by a crusher. It is generally controlled between a few millimeters and a few centimeters to increase its specific surface area and improve the rate and efficiency of the pyrolysis reaction. Batch pyrolysis plants can process packaged plastics.
Pyrolysis of Mixed Plastic Waste
After pretreatment, plastic waste enters the pyrolysis stage. This is the core link of the entire plastic pyrolysis plant.
The pyrolysis reaction is carried out in a specially designed pyrolysis reactor. The rotary kiln reactor uses a rotating cylinder to slowly move the plastic raw materials in the kiln and fully contact the heating medium to complete the pyrolysis reaction. Workers need to accurately control the plastic pyrolysis process parameters according to different types of plastics and pyrolysis targets.
During the pyrolysis of mixed plastic waste reaction, process parameters such as temperature, pressure, and reaction time have a significant impact on the composition and properties of the products.
Generally speaking, increasing the pyrolysis temperature will increase the amount of gas products generated, while shortening the molecular chain of liquid oil and increasing the content of light components. Prolonging the reaction time helps to increase the degree of decomposition of plastics, but too long a reaction time may cause excessive cracking of the product and reduce the yield of the target product.

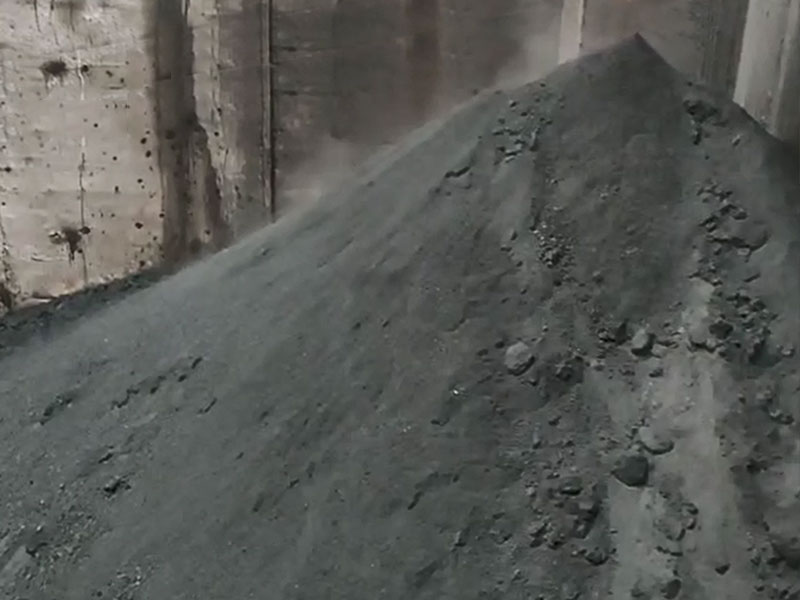
Plastic Pyrolysis Product Collection
After the pyrolysis of mixed plastic waste is completed, the product collection stage will follow. The main task of this stage is to effectively separate and collect the gas, liquid and solid three-phase products produced by pyrolysis.
The gas and oil vapor produced during the plastic pyrolysis process first enter the condensation system. They condense the gaseous oil vapor into liquid oil through the action of cooling media (such as water or air) to achieve gas-liquid separation.
- The condensed liquid oil can be converted into diesel or gasoline fractionation after further refining treatment, such as pyrolysis oil distillation equipment.
- The uncondensed gases are mainly non-condensable gases such as hydrogen and methane. These gases have a high calorific value and can be transported to combustion equipment through pipelines as fuel for heating or power generation.
- The solid residue produced by pyrolysis is mainly carbon black, which remains at the bottom of the reactor and is discharged through the slag discharge system.