Pyrolysis equipment, as the key carrier for the realization of pyrolysis technology, supports the wide application of pyrolysis technology in various fields. Common pyrolysis equipment types are rich and varied.
The core components and key systems in the pyrolysis plant play a vital role in the realization of pyrolysis technology. Every component and system of the pyrolysis equipment works closely together to ensure that the pyrolysis technology can operate stably and efficiently.
Core Equipment of Pyrolysis Technology
Take the waste tire continuous pyrolysis plant as an example. The feeding system includes a conveyor and a crusher, which work together. The crusher crushes the waste tire size to less than 5-8mm, so that it meets the conditions suitable for continuous pyrolysis. The conveyor can smoothly transport large pieces of tires to the crusher and then to the pyrolysis reactor.
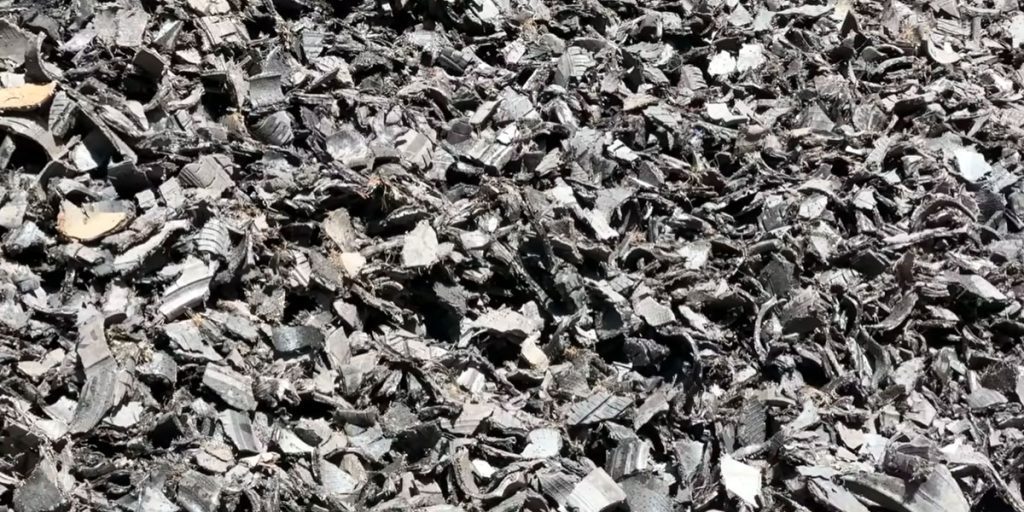
The pyrolysis reactor is the core of the entire tire pyrolysis plant. It heats the waste tires at high temperature in an oxygen-deficient or oxygen-free environment to decompose them into products such as pyrolysis oil, carbon black, syngas and steel wire.
The heating system provides energy for the pyrolysis reactor and provides the required high temperature environment for the pyrolysis process. The initial heating fuel can be natural gas, diesel, pyrolysis oil, etc. To ensure that the energy can be fully utilized during the reaction process, syngas can be used as a heating energy source in the later stage.
The condensation system converts the oil and gas produced during the tyre pyrolysis process into liquid pyrolysis oil. The condenser is a key component, which usually uses water cooling or air cooling to convert high-temperature oil and gas into valuable liquid fuel.
The gas treatment system processes the non-condensable gases produced by pyrolysis to ensure that the emissions meet the standards. It includes dust collectors, desulfurization devices, etc., which can effectively remove harmful gases and particulate matter.
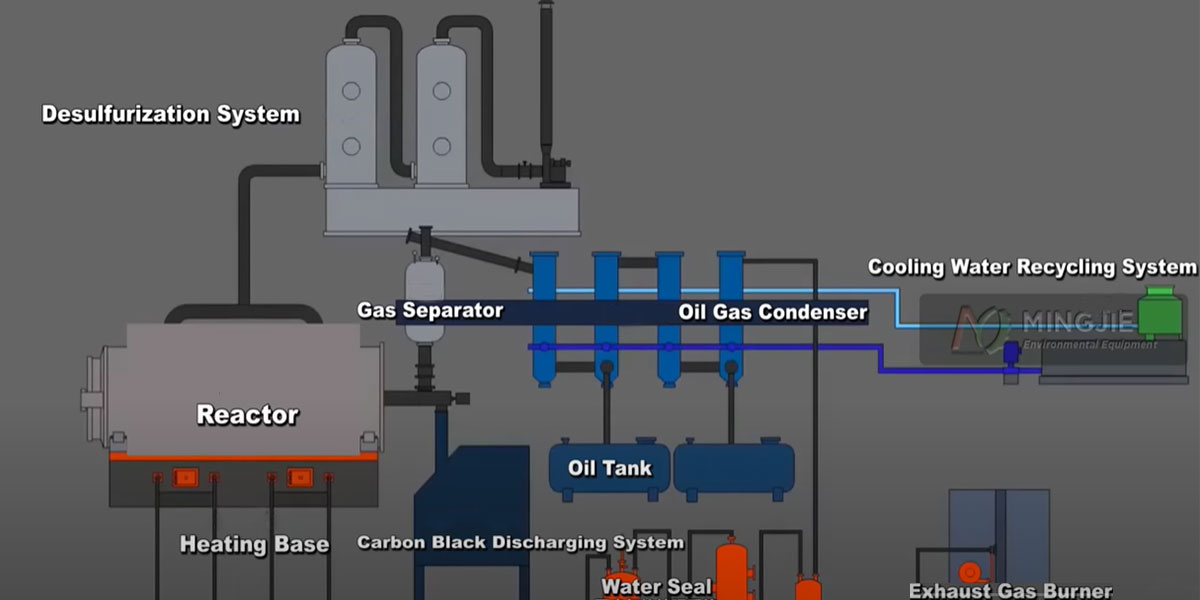
The solid treatment system is used to treat solid residues such as carbon black and steel wire produced after pyrolysis. Carbon black can be further processed into industrial products. Steel wire can be recycled and reused to maximize the utilization of resources.
Impact of Pyrolysis Technology on Equipment
The unique characteristics of pyrolysis technology have a profound impact on the design and manufacture of pyrolysis equipment. Pyrolysis technology can convert organic matter in solid waste into fuel gas, fuel oil and carbon black. This feature determines that when designing pyrolysis equipment, full consideration must be given to how to achieve this conversion efficiently.
In the design of biomass pyrolysis equipment, in order to improve the efficiency of biomass conversion into biochar, R&D personnel will carefully design the structure of the pyrolysis reactor.
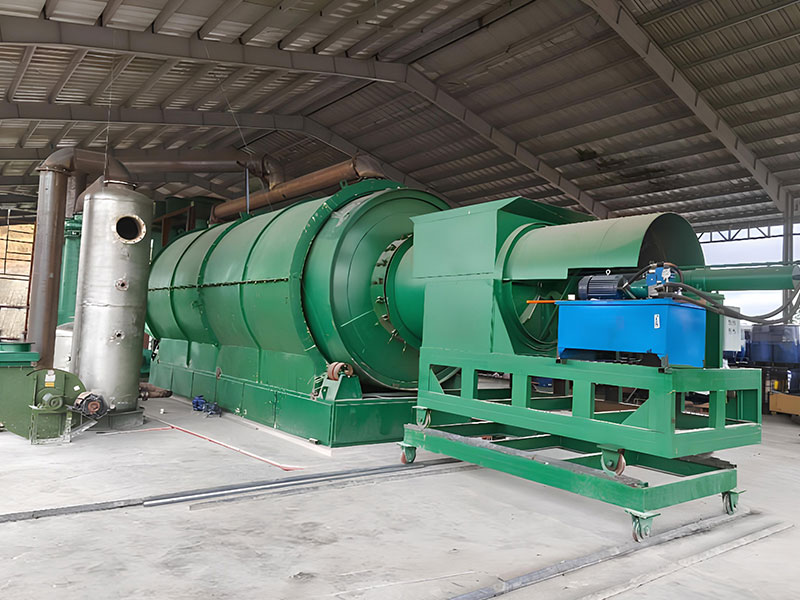
The pyrolysis process is carried out under the conditions of anaerobic decomposition, which makes the exhaust volume small and helps to reduce secondary pollution to the atmospheric environment. Based on this feature, when designing pyrolysis equipment, the focus will be on the sealing and gas treatment system of the equipment.
For pyrolysis in solid waste management, the MSW pyrolysis equipment adopts materials and structural designs with good sealing performance. At the same time, it is equipped with an efficient gas purification system to treat the small amount of waste gas generated by pyrolysis. Remove harmful substances in it to meet environmental emission standards.
Pyrolysis technology has high requirements for equipment, slow reaction speed, and difficult control of operating conditions. These characteristics require the use of high-quality materials and advanced manufacturing processes when manufacturing pyrolysis equipment.
Pyrolysis reactors are usually made of high-temperature and corrosion-resistant alloy materials to withstand the erosion of high temperatures and corrosive gases. In the design of the equipment control system, advanced automatic control technology is used to achieve precise control of parameters such as reaction temperature, pressure, and feed rate.
Intelligent sensors are used to monitor various parameters in the reaction process in real time. The operating status of the equipment is automatically adjusted through the computer control system to ensure that the pyrolysis reaction is carried out under optimal conditions.
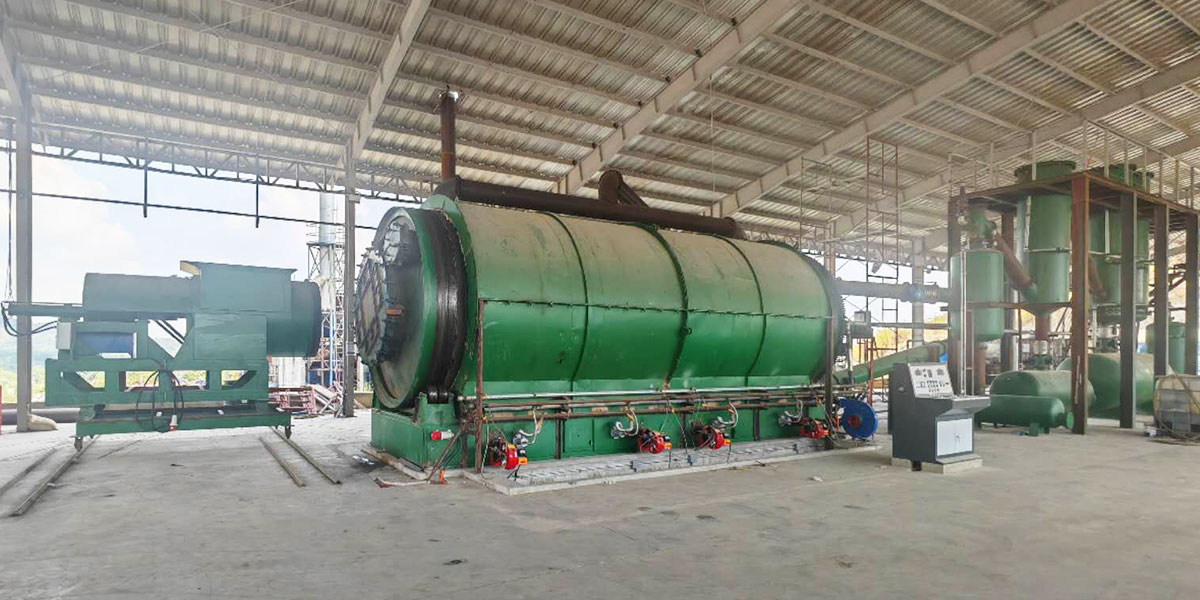
Application of Pyrolysis Plant
In terms of organic hazardous waste treatment, the advantages of pyrolysis technology and equipment are very obvious. For example, when using pyrolysis plant to treat medical waste, these organic hazardous wastes are decomposed under high temperature and oxygen-free conditions. The combustible gas and pyrolysis oil produced can be recycled as fuel. The harmful substances in the solid residue are fixed and can reach the harmless standard after treatment.
Pyrolysis is a thermochemical process. It uses the thermal instability of organic matter to heat it in an oxygen-free or oxygen-deficient environment to cause a decomposition reaction. When organic matter is heated to a certain temperature, the chemical bonds in the molecules begin to break, and complex organic molecules gradually decompose into smaller molecules.
In the pyrolysis equipment, large molecular organic matter will gradually convert into three-phase products of gas, liquid and solid. According to the heating rate and residence time, pyrolysis equipment can be divided into slow pyrolysis and fast pyrolysis types.
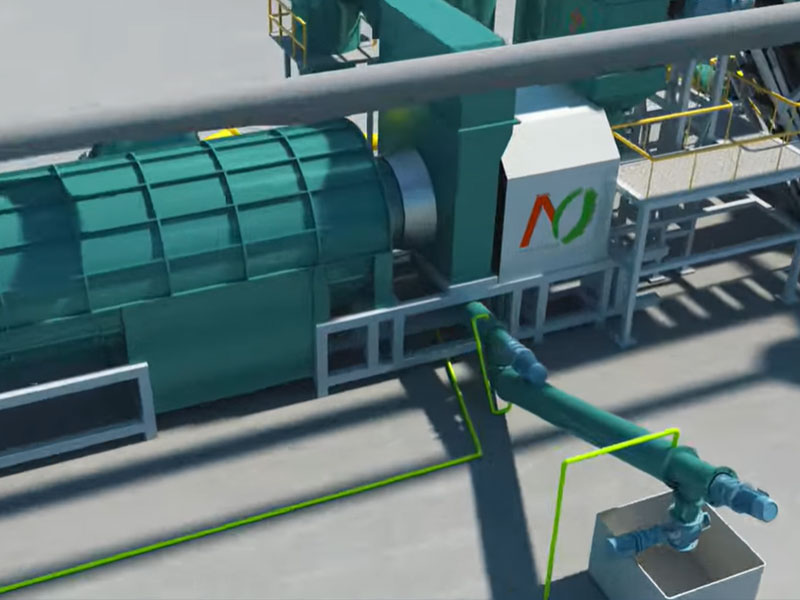
Slow pyrolysis uses a lower heating rate (about 0.1 – 1°C per second). It heats the material slowly, and the material stays in the equipment for a relatively long time, ranging from a few minutes to a few hours. In this slow process, the main products are coke (solid residue) and a small amount of liquid (bio-oil) and gas (synthesis gas). This pyrolysis equipment is often used for biochar production. Because it can produce a high content of coke, these cokes can be used in industrial production or added to soil to improve soil structure.
Fast pyrolysis is carried out at a higher heating rate and a shorter steam residence time, which is conducive to the generation of liquid products (pyrolysis oil). These pyrolysis oils can be further refined into diesel or gasoline base oils through distillation equipment. The fast pyrolysis is suitable for tire/plastic/medical waste/MSW/oil sludge pyrolysis.
Pyrolysis of Waste Plastic
In the pyrolysis reactor, as the temperature rises, the waste plastics gradually decompose into liquid fuel, synthesis gas and solid carbon black. These products have high utilization value. Synthesis gas such as ethylene and propylene are important chemical raw materials. Liquid pyrolysis oil can be used as fuel oil. Carbon black is widely used in rubber, ink, coating and other industries.
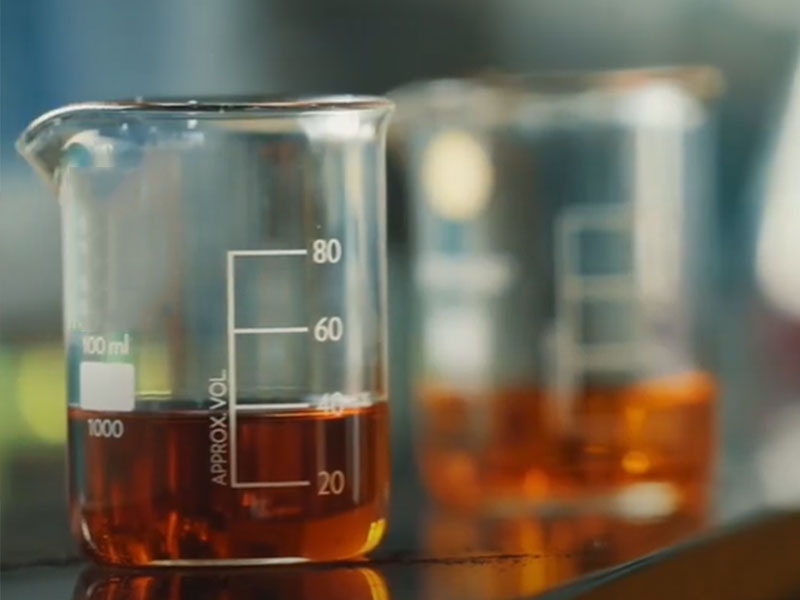
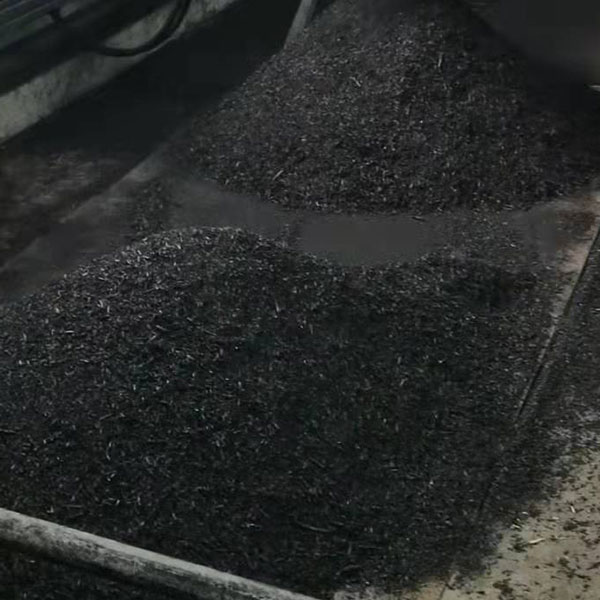
Biomass Pyrolysis
In the biomass pyrolysis machine, the cellulose, hemicellulose and lignin components of biomass will decompose respectively to form synthesis gas, bio-oil and biochar. This process is essentially different from combustion. Combustion is a violent oxidation reaction under aerobic conditions, which will produce a large amount of carbon dioxide and water. Pyrolysis is carried out in an anaerobic or anoxic environment, focusing more on the decomposition and transformation of substances.
Summary
Although pyrolysis technology and pyrolysis plant have shown great potential and advantages in many fields. However, they also face many challenges in their development process.
On the technical level, the complexity of the pyrolysis process makes it a big problem to accurately control the reaction conditions. Pyrolysis reactions involve a variety of chemical reactions and physical processes. Slight changes in parameters such as reaction temperature, heating rate, and residence time may have a significant impact on the composition and properties of pyrolysis products.
Cost issues are also an important factor restricting the widespread application of pyrolysis technology and equipment. The initial investment cost of pyrolysis equipment is high, which is a considerable burden for some companies and projects with limited funds.
With the gradual rise of the pyrolysis technology and pyrolysis plant market, more and more companies and institutions have joined in, and market competition is becoming increasingly fierce. This has brought both the impetus for technological innovation and product optimization and huge pressure on companies. In the field of pyrolysis plant manufacturing, products from different companies differ in performance, quality, and price.