The pyrolysis tire recycling system realizes the recycling of waste tires through pyrolysis technology. The tire pyrolysis plant solves the problem of a large amount of waste tires accumulating. At the same time, the tire pyrolysis products (pyrolysis oil and recycled carbon black) also bring more profits to the tire pyrolysis project.
The working principle of the pyrolysis tire recycling system is based on pyrolysis technology. This is a process in which organic polymer compounds in waste tires undergo cracking reactions at high temperatures in an oxygen-free or low-oxygen environment.
In this tire pyrolysis process, waste tires are heated to a specific temperature. The chemical bonds inside them break, and the macromolecular structure gradually decomposes and transforms into small molecules. Ultimately, a variety of valuable products such as fuel oil, carbon black, steel wire, and combustible gas are produced.
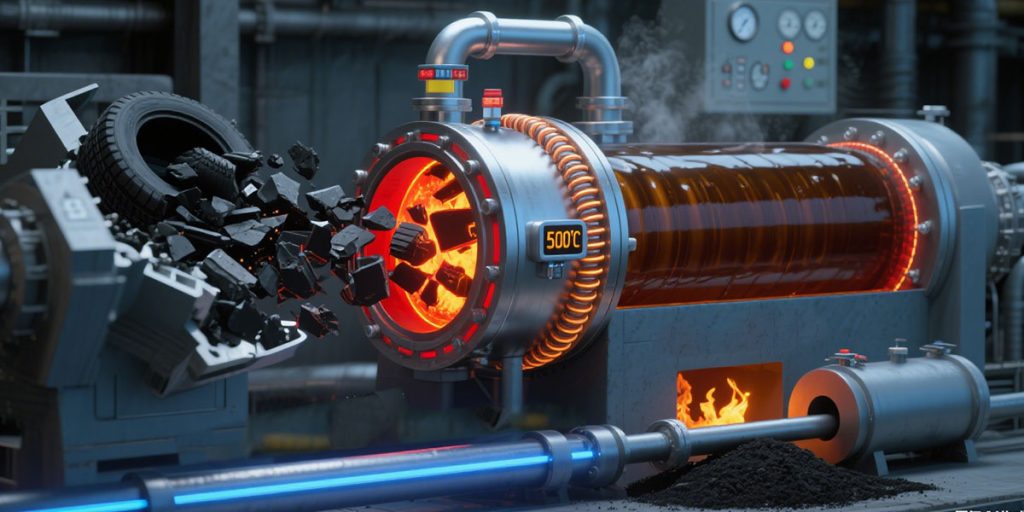
Advantages of Pyrolysis Tire Recycling System
The pyrolysis tire recycling system provides an innovative and more environmentally responsible solution to maximize the entire life cycle of tires. According to statistics, about 1 billion tires reach the end of their service life every year. The waste tire pyrolysis project is an important part of its strategy to promote the circular economy and sustainable development.
The tire pyrolysis plant realizes the effective recycling of resources. Waste tires contain rich resources, and these resources can be redeveloped and utilized through pyrolysis technology.
The four main products produced by tire pyrolysis are: fuel oil, recovered carbon black (rCB), steel wire and synthesis gas. The latter two outputs are called by-products.
Steel wire can also be separated and recycled as a raw material for steelmaking, realizing the recycling of metal resources. Syngas can be used as a supplementary energy source for the tyre pyrolysis equipment to achieve energy recycling.
However, fuel oil and rCB are products with great commercial potential.
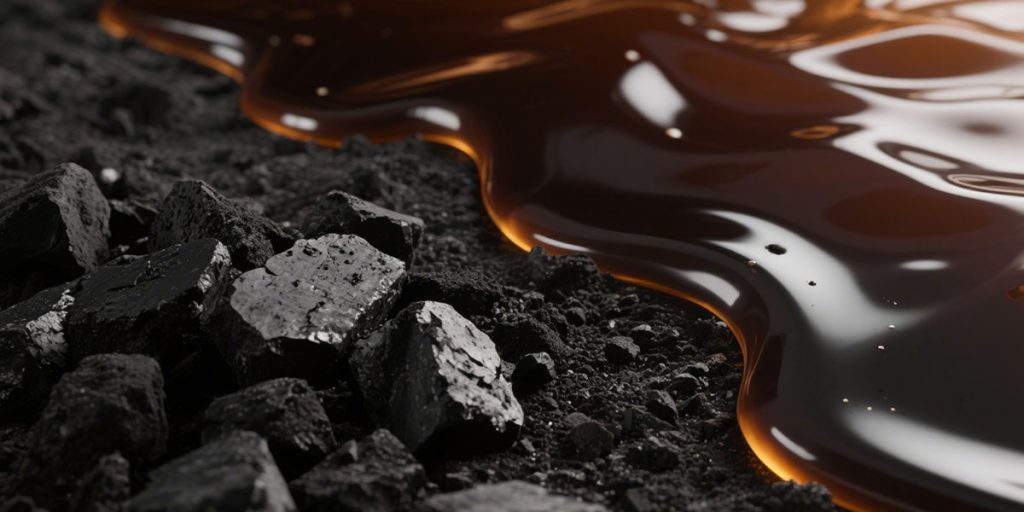
Tire To Oil (TPO)
The rubber in the tire can be converted into Tire To Oil (TPO). During the tire pyrolysis process, oil accounts for about 40-45% of the output by weight. The main uses of tire pyrolysis oil are: marine fuel, vehicle engine fuel.
Tire pyrolysis oil can be used as industrial fuel or further refined into gasoline and diesel by distillation plant, providing a new resource supplement for the energy field.
Recycled Carbon Black (rCB)
The carbon black in the tire can be recycled and reused to make rubber products, inks, coatings. This reduces the demand for virgin carbon black.
Recycled carbon black (rCB) accounts for approximately 30% to 35% of tire pyrolysis production. Tire-derived recycled carbon black (rCB) is an economically attractive and valuable product. In order to make it marketable, post-pyrolysis processing steps may be required. The purity of the final product and the amount of processing required will have a significant impact on the value of the rCB.
How to Achieve the Tyre Waste Recycling by Pyrolysis
Mingjie Group provides 2 modes (batch and continuous) of pyrolysis tire recycling system to realize the tire pyrolysis recycling.
Batch Pyrolysis Tire Recycling
The batch pyrolysis tire recycling system can process whole tires. There is no need to wash, crush, or wire draw the tires. Used tires can be put into the pyrolysis furnace manually or automatically by the hydraulic loader. The hydraulic feeding process is highly automated, safe, convenient, and time-saving.
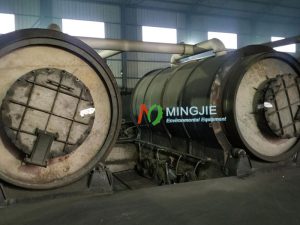
Pyrolysis reaction is the core step to achieve the recycling of waste tires. The pyrolysis tire recycling system will seal the reactor filled with pre-treated tires, and then introduce inert gas (such as nitrogen) to exhaust the air in the reactor to create an oxygen-free or low-oxygen environment.
The reactor is then heated by a heating device. When the temperature reaches a certain level (usually 300-600℃), the organic polymer compounds in the tire begin to undergo a cracking reaction. In this process, the tire gradually decomposes into products such as fuel oil, carbon black, steel wire and combustible gas.
These tire pyrolysis products are the key to recycling. They will be further processed and utilized to complete the transformation of tires from waste to reusable resources.
After the reaction is completed, it enters the cooling and separation stage. The mixed gas produced by cracking passes through the cooling system, and the fuel oil component in it will condense into liquid and be collected.
The uncondensed combustible gas can be collected through a special pipeline, and a part of it can be used as fuel for the pyrolysis tire recycling system itself to heat and realize energy recycling. The other part can also be used as fuel for other industrial production after treatment.
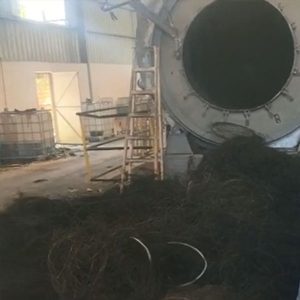
At the same time, the solid products remaining in the reactor include carbon black and steel wire. After separation and purification, the steel wire can be directly recycled and sent to the steel plant to be re-smelted into new steel. The carbon black is further processed.
The last step is to clean the pyrolysis reactor. Clean up the remaining residue in the reactor and prepare for the next batch of waste tires.
Continuous Pyrolysis Tire Recycling
The core of the fully continuous pyrolysis tire recycling system to realize the recycling of waste tires lies in its coherent and automated processing process.
The pretreatment stage is the beginning of the pyrolysis tire recycling system, including pulling out steel wire and crushing into fine tire fragments. The pyrolysis process is an important stage in the conversion of waste into pyrolysis oil, synthesis gas and carbon black.
The waste tire pyrolysis carbon black is cooled and discharged through a spiral water-cooled slag removal system.
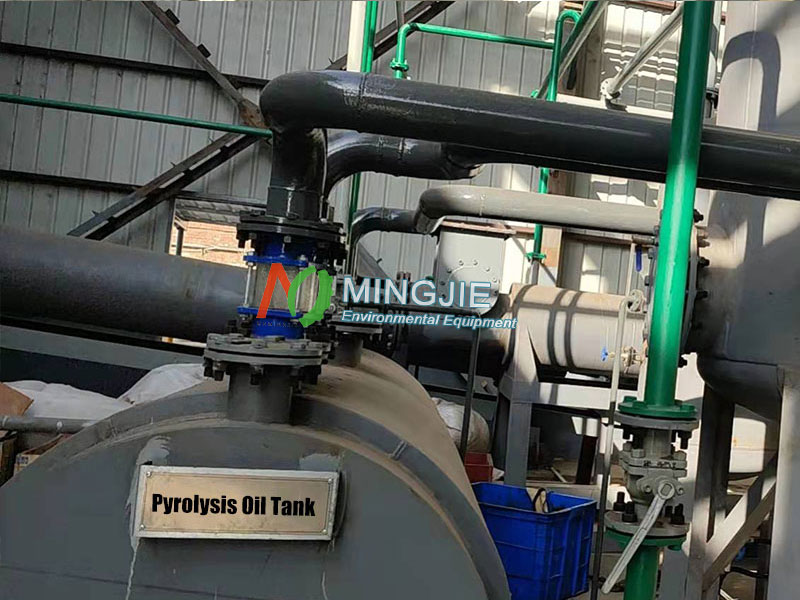
The pyrolysis product oil and gas pass through a buffer tank and then enter a high-efficiency condensation system. The final condensed oil, also known as tire pyrolysis oil (TPO)/tire derived fuel (TDF), is collected in an pyrolysis oil tank.
The non-condensable gas remaining after condensation is purified by the exhaust gas purification system and then returned to the pyrolysis reactor as a heating source. The flue gas discharged from the furnace is purified by a desulfurization tower and discharged into the atmosphere in accordance with environmental protection standards.
The continuous pyrolysis tire recycling system adopts an intelligent operation and control PLC system. This monitors and counts the stages of the continuous pyrolysis of waste tires into fuel oil production process in real time, achieving precise feed, temperature and pressure control.