Both tyre pyrolysis machine and plastic pyrolysis machine are based on pyrolysis technology, which can convert organic materials into fuel oil or carbon black. However, due to differences in raw material composition and process requirements, plastic and tire pyrolysis equipment have significant differences in design, processing flow and products.
The differences between waste plastic pyrolysis plant and tyre pyrolysis plant mainly include differences in pretreatment system, pyrolysis system, emission purification system.
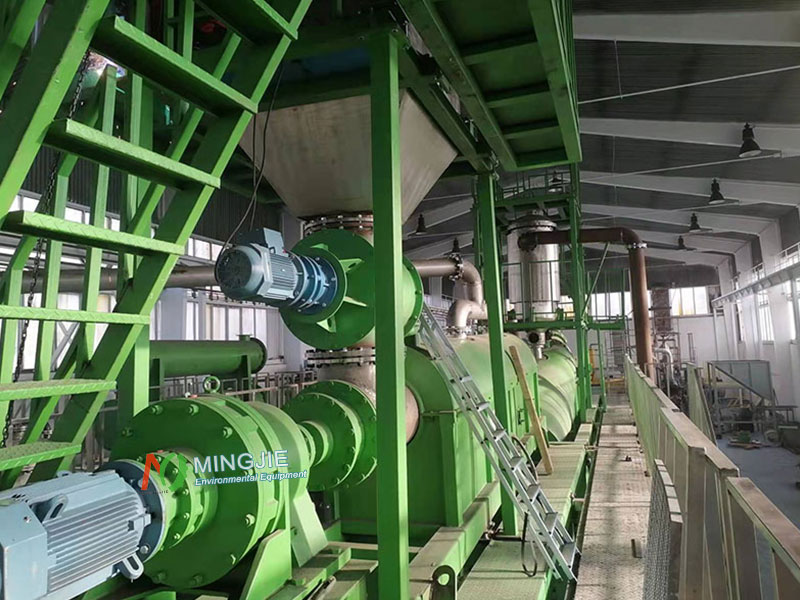
Differences in Pretreatment System
Waste Plastic Material
There are many types of plastics, the most common ones are polyethylene (PE), polypropylene (PP), polystyrene (PS), polyvinyl chloride (PVC), etc.
Plastics come in various forms, including films, pipes, plates, injection molded parts, etc. Plastics are relatively soft and generally do not contain metal components. Waste Plastic Pyrolysis Pretreatment is relatively simple, with preliminary treatments such as cleaning and crushing.
Note: Polyvinyl chloride (PVC) and polyethylene terephthalate (PET) plastics are not suitable for pyrolysis.
PVC contains chlorine, which releases harmful HCl gas during the pyrolysis of PVC plastics. Hydrogen chloride gas corrodes equipment, harms the environment, and poses a risk to workers’ health. PVC pyrolysis oil still contains Cl. When burned, it releases dioxin, a highly toxic carcinogenic compound.
PET produces almost no pyrolysis oil. The resulting product is mostly a low-quality powdery residue with low economic value. PET pyrolysis releases oxygen, it reacts with combustible gases and there is a risk of explosion.
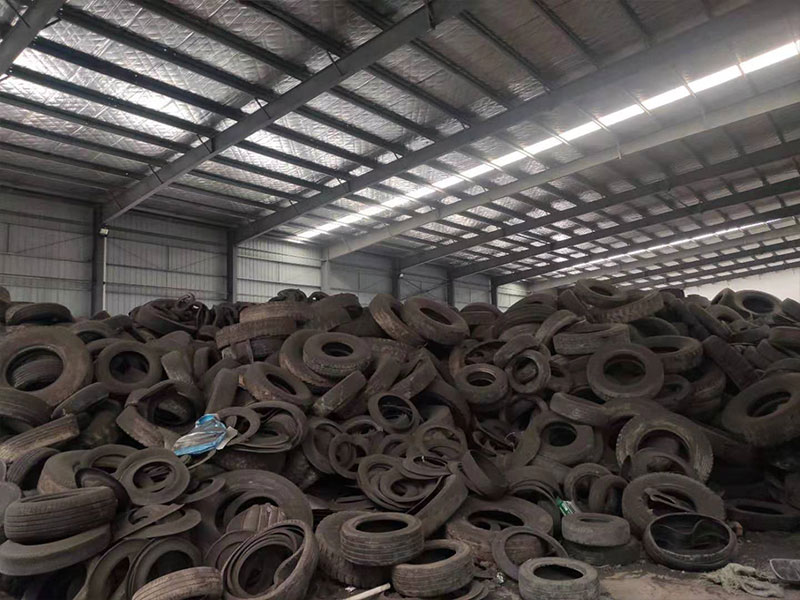
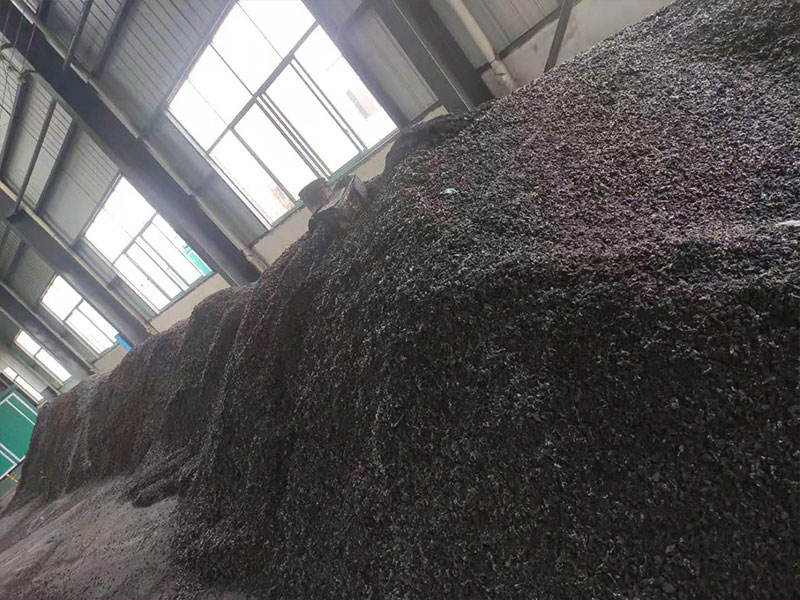
Scrap Tire Mechanical Recycling
Tires are mainly composed of natural rubber, synthetic rubber, carbon black, steel wire and a variety of additives. Scrap tyre has a complex structure, tough texture and contains steel wire. This requires mechanical recycling of tires before pyrolysis, such as cutting, crushing and removing steel wire.
Differences in Plastic and Tyre Pyrolysis Machine Design
Pyrolysis Reactor
Tire recycling pyrolysis reactor requires wear-resistant design and enhanced stirring devices, so as to handle steel wire and solid residues.
The temperature of scrap tire pyrolysis is generally 400-600 degrees Celsius. Due to the complex composition of tires, the pyrolysis reaction time is usually longer, and rubber and carbon black need to be more fully decomposed.
Plastic pyrolysis reactors focus on sealing and corrosion resistance, in order to prevent gas leakage and deal with acidic gases.
The temperature of waste plastic pyrolysis is generally around 300-500 degrees Celsius. The pyrolysis reaction time of plastics is relatively short, depending on the type of plastic. Plastics pyrolyze faster, but the temperature needs to be controlled to prevent coking.
The heating method of waste tire and plastic pyrolysis reactors is the same: gas burner heating or electric heating.
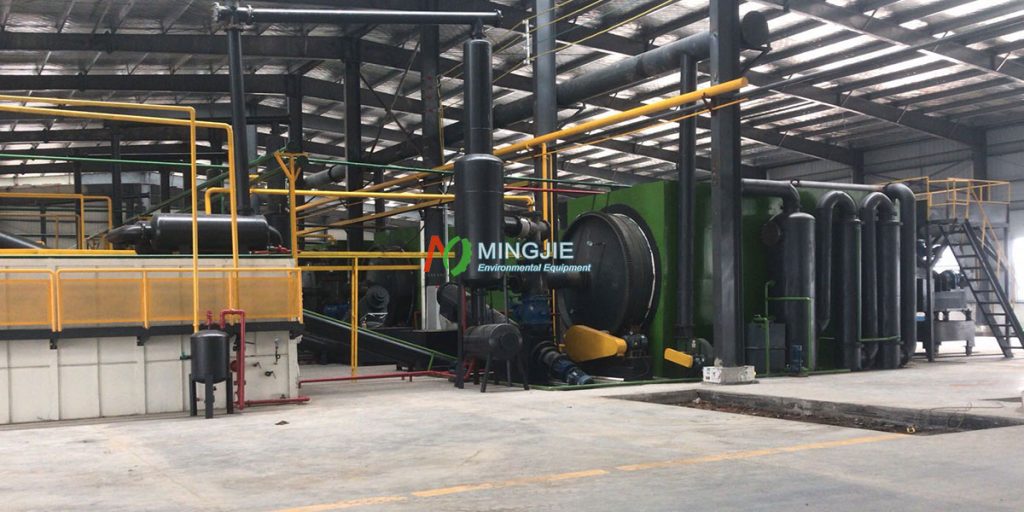
Condensation System
The oil and gas produced by tire pyrolysis recycling are complex and contain more impurities and high-boiling substances. The condensation system needs to have higher condensation efficiency and separation capabilities.
The oil and gas produced by waste plastic pyrolysis are relatively pure, with fewer impurities and high-boiling substances. The condensation system is relatively simpler.
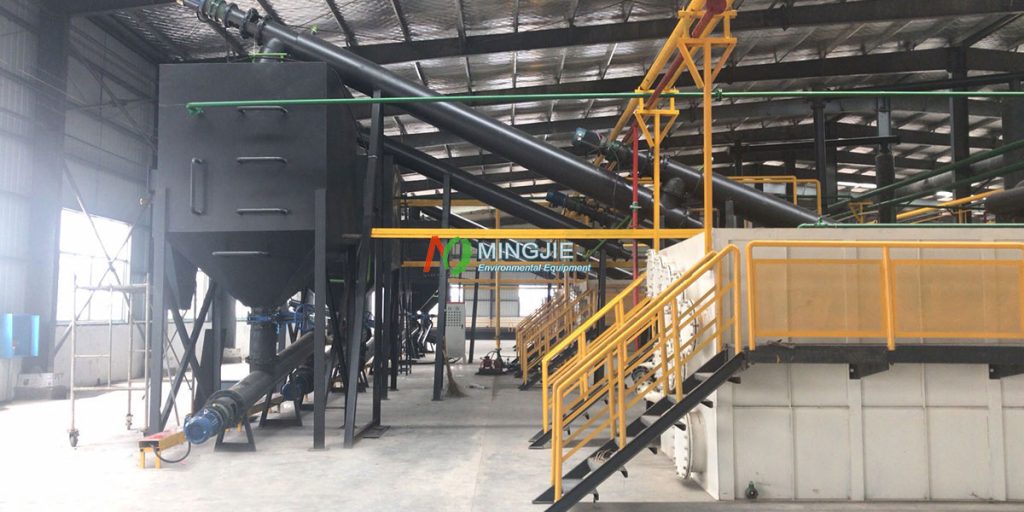
Emission Purification System
The products of tire recycling pyrolysis plant include carbon black, steel wire, pyrolysis oil and syngas. The gas treatment system is relatively complex, including dust collector and desulfurization device. In order to remove harmful gases and particulate matter in the non-condensable gas produced by pyrolysis, so that it can meet the emission standards.
The products of waste plastic pyrolysis plant are mainly pyrolysis oil, pyrolysis gas and solid residue. Pyrolysis oil can be used as fuel or further processed into chemical raw materials. Pyrolysis gas can usually be used as fuel gas after simple purification treatment. The amount of solid residue is relatively small.
Conclusion
If mixed waste (tire + plastic) needs to be processed, the pyrolysis equipment needs to be customized, but the production efficiency may be reduced. It is recommended to select the corresponding pyrolysis equipment according to the main raw material type.