In the field of plastic solid waste treatment, pyrolysis for plastic recycling has demonstrated a strong ability to handle complex plastics, which is difficult for mechanical recycling to achieve. Pyrolysis plant can directly process mixed plastics.
Mixed plastics are very common in plastic solid waste. For example, many food packaging bags in daily life are made of a variety of plastics such as polyethylene (PE) and polypropylene (PP). The composition of these mixed plastics is complex, and the different components are closely combined. In the process of mechanical recycling, it is difficult to accurately separate these different types of plastics, which makes recycling extremely difficult. Even if the recycling is successful, the quality of the recycled plastics is difficult to guarantee.
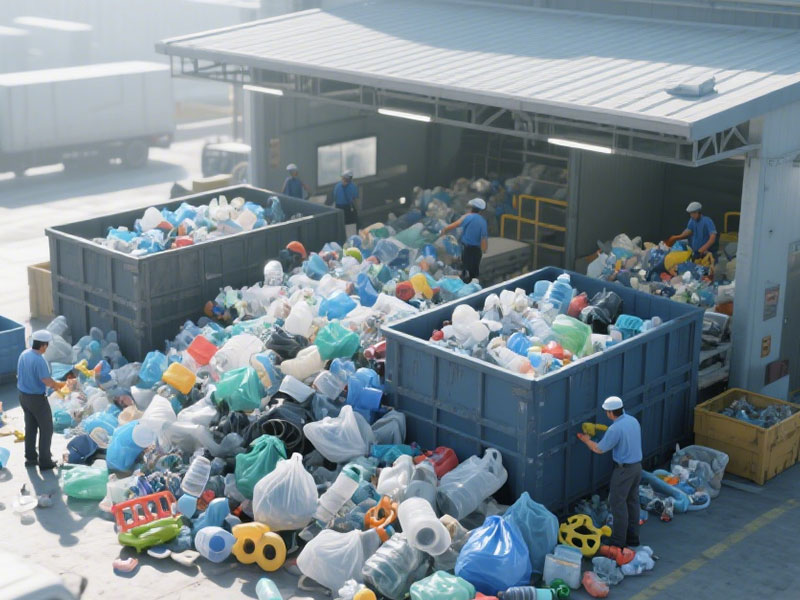
During the operation of the plastic pyrolysis equipment, high temperature will break the molecular chains of the mixed plastics and decompose them into small molecules. When the pyrolysis plant processes mixed plastics composed of PE and PP, the molecular chains of PE and PP will break under the action of high temperature. Then it is converted into plastic pyrolysis oil, carbon black and synthesis gas. These plastic pyrolysis products can be further collected and utilized, realizing the effective recycling of mixed plastics.
Solid waste handlers and recyclers avoid using PVC and PET plastics in the pyrolysis for plastic recycling. Because its pyrolysis process produce harmful by-products.
Why Choose Pyrolysis For Plastic Recycling
Large chemical companies are backing pyrolysis plants to convert plastic waste into hydrocarbon feedstocks that can then be processed back into plastics. They believe the pyrolysis for plastic recycling method can recover more plastics than conventional mechanical recycling.
Petrochemical manufacturers are fully supporting the various pyrolysis processes being developed around the world. Almost all of the large chemical companies – such as Dow, BASF, Shell, ExxonMobil, LyondellBasell Industries, Saudi Basic Industries Corp., Ineos, Petrobras and Total Energy – have either partnered with smaller companies to develop processes or are developing them themselves.
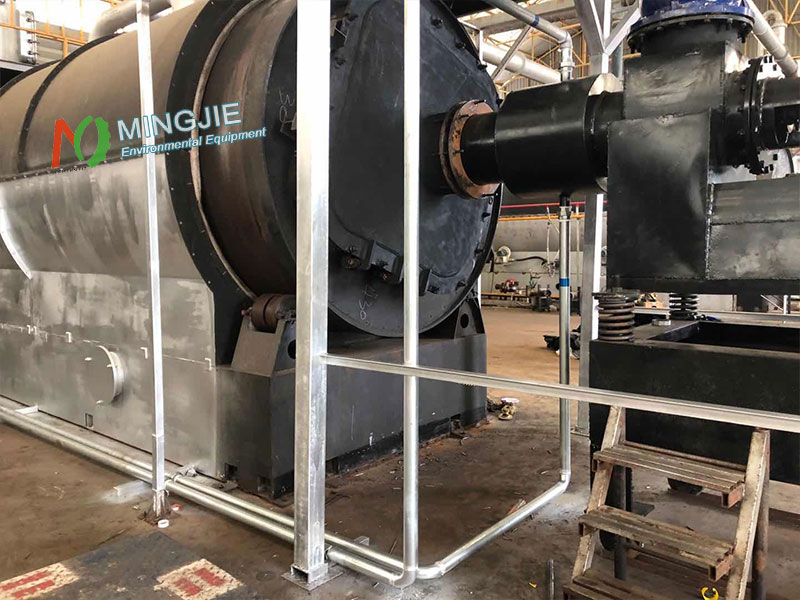
These large chemical companies support pyrolysis plants not only out of environmental responsibility, but also because they see the broad prospects of pyrolysis for plastic recycling. Pyrolysis technology can process complex plastics, improve the purity and quality of recycling, and bring significant environmental benefits. These advantages of plastic recacling pyrolysis are highly consistent with the goals of chemical companies to pursue sustainable development, expand business areas, and enhance corporate competitiveness.
Pyrolysis for plastic recycling is an effective waste management method. It not only reduces landfill waste, but also produces valuable by-products such as bio-oil, syngas and biochar. Compared with incineration, plastic pyrolysis minimizes harmful emissions. It reduces greenhouse gas emissions by reducing dependence on fossil fuels and promotes a circular economy through material recovery.
Mingjie Group provides distillation equipment to improve the quality of plastic pyrolysis oil, making the output of plastic pyrolysis systems cleaner and more reliable.
Co-development of Ppyrolysis and Mechanical Recycling
Mechanical and pyrolysis for plastic recycling are not isolated from each other, but can complement each other and develop synergistically. They jointly build a more complete plastic recycling system. According to the characteristics and recycling requirements of plastic waste, the reasonable selection of pyrolysis technology and mechanical recycling technology can achieve the maximum recycling and utilization of plastic solid waste.
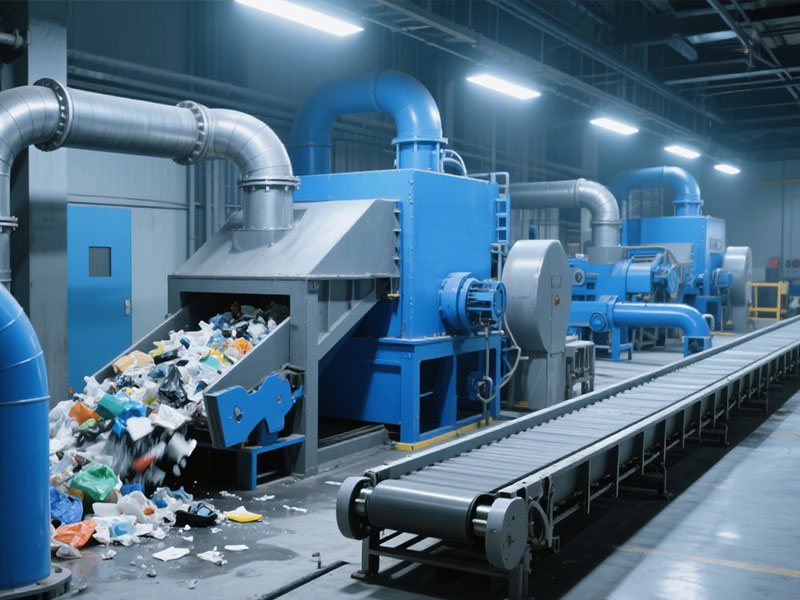
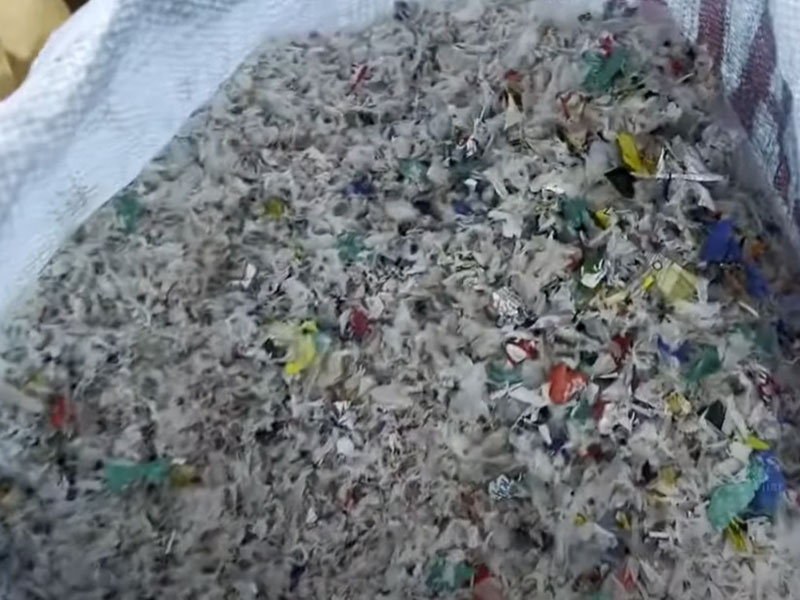
For some plastic wastes with higher purity and less pollution, mechanical recycling is still an efficient and economical recycling method. Through mechanical recycling, these plastic wastes can be directly converted into recycled plastic particles for the production of new plastic products. For some single types of plastic containers, mechanical recycling can quickly and cost-effectively achieve the reuse of plastics.
For those mixed plastics, severely contaminated plastics and some special plastics that are difficult to process through mechanical recycling. The pyrolysis for plastic recycling can be used for treatment. Pyrolysis technology can convert these complex plastic wastes into valuable energy and chemical raw materials to achieve the recycling of resources.
In some large plastic recycling plants, attempts have been made to combine pyrolysis technology with mechanical recycling technology. First, the plastic waste is preliminarily screened and classified, and the plastics suitable for mechanical recycling are separated and mechanically recycled.
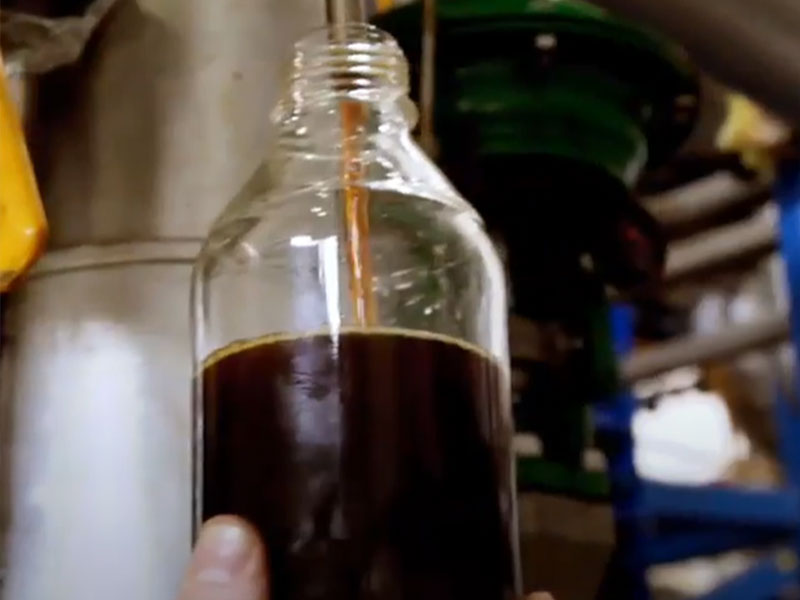
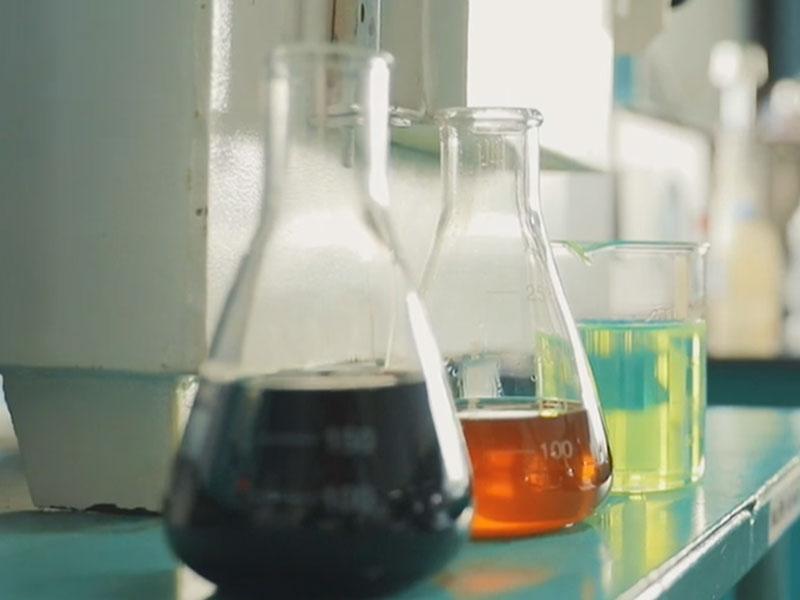
For the remaining plastics that are difficult to recycle mechanically, they are sent to the plastic pyrolysis equipment for pyrolysis treatment. The pyrolysis oil and synthesis gas products produced by pyrolysis can be further processed and utilized, and the solid residue after pyrolysis can also be recycled. In this way, not only the recycling rate of plastics is improved, but also the recycling cost is reduced and the pollution to the environment is reduced.
The coordinated development of mechanical and pyrolysis for plastic recycling can also promote the improvement of the plastic recycling industry chain. The chemical raw materials produced by pyrolysis technology can provide a new source of raw materials for plastic production enterprises and realize the closed-loop production of plastics. The recycled plastic particles produced by mechanical recycling can be used to produce various plastic products to meet the market demand for plastic products.