Car tyre recycling refers to the recycling of tires that have reached the end of their service life or can no longer be used. Tire processing can be converted into reusable resources or products through physical, chemical or biological methods. The tire to oil pyrolysis plant can convert waste tires into pyrolysis oil (WTPO) with high calorific value (41.63 MJ/kg) through chemical pyrolysis technology.
Pyrolysis is considered one of the important technologies for waste tire disposal. The main products of pyrolysis include pyrolysis oil, syngas, carbon black and steel wire. Pyrolysis oil is the most valuable product of waste tire pyrolysis and has the potential to be a substitute for traditional fuels.
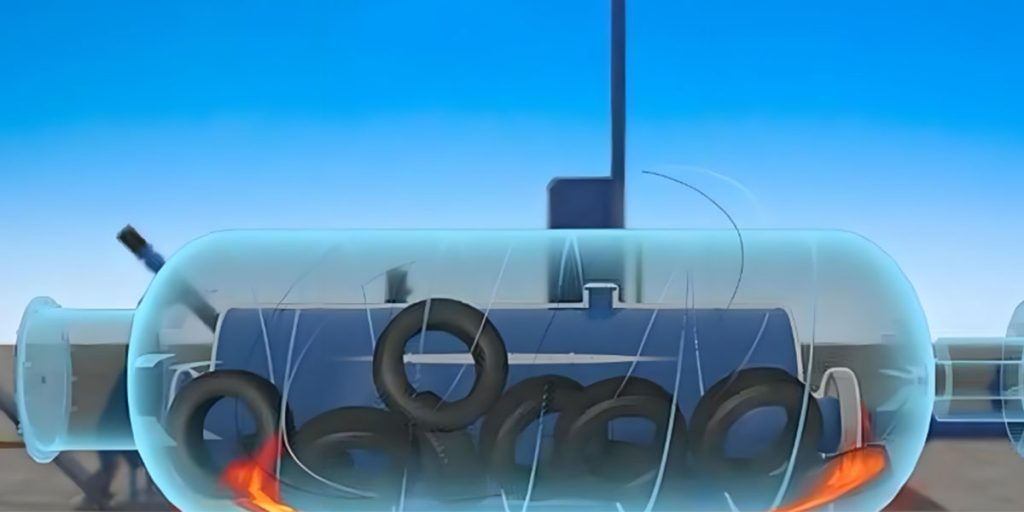
Waste Tire to Oil Pyrolysis Market
As an emerging and highly promising field, waste tire pyrolysis to produce fuel oil has shown a booming development trend worldwide in recent years.
In terms of market size, the global tire pyrolysis oil market size in 2023 is approximately US$43.1 million. With the continuous advancement of technology and the continued growth of market demand, this figure is expected to climb to US$88.9 million by 2030.
In terms of tire pyrolysis oil sales, it also shows a strong upward trend. Global tire pyrolysis oil sales in 2023 are considerable, and it is expected to achieve significant growth by 2030.
With its developed automobile industry and perfect tyre recycling system, North America has become the world’s largest waste tire to oil pyrolysis market, accounting for about 39% of the market share. Many well-known pyrolysis oil manufacturers have taken root here, such as Reoil and Bolder Industries. They continue to invest in research and development, improve the level of pyrolysis technology, and expand the scale of waste tire to oil pyrolysis plants.
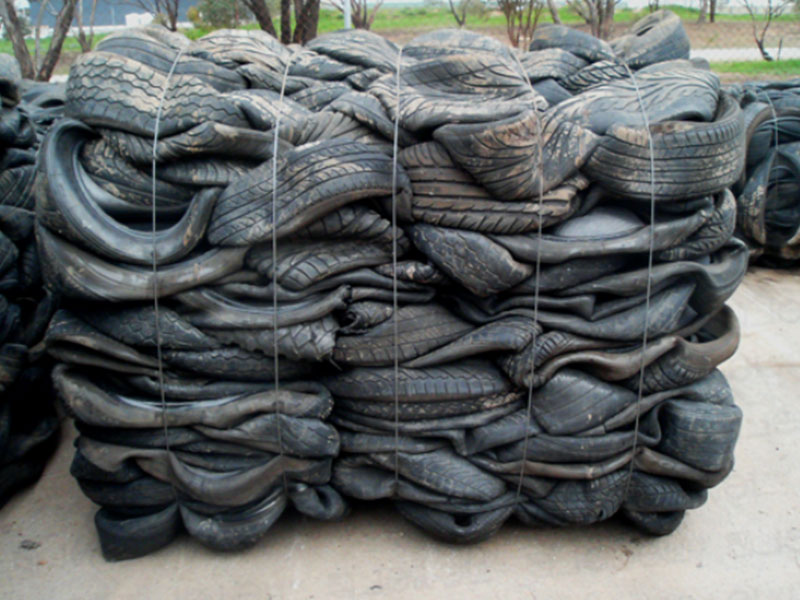
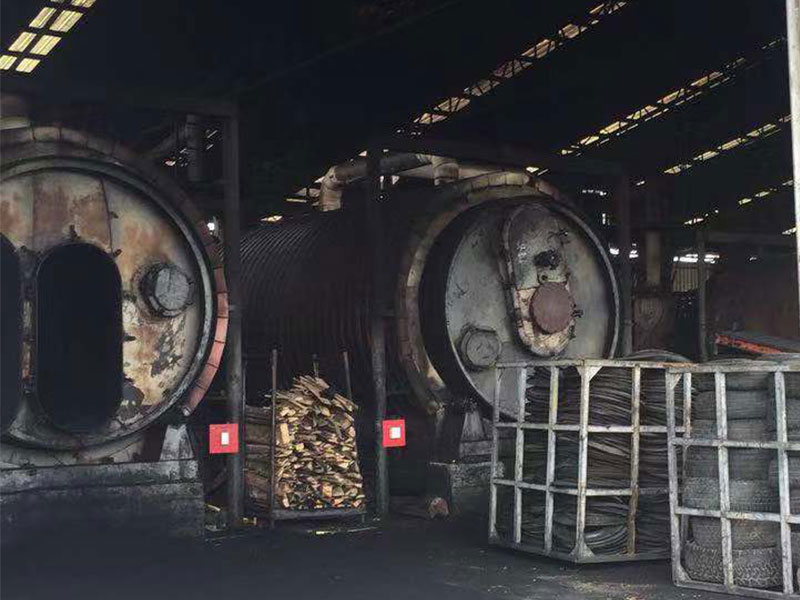
The waste tire to oil pyrolysis market in the Asia-Pacific region accounts for about 31%. With the rapid development of the national economy, the number of cars has continued to increase, and the amount of car waste tires has also increased accordingly, providing abundant raw materials for the pyrolysis plant. At the same time, these countries have continuously increased their attention to environmental protection and resource recycling, and have introduced a series of supporting policies to promote the development of the pyrolysis oil market.
The European tire to oil pyrolysis market accounts for 22% of the market share. Europe has always been at the forefront of the world in terms of environmental protection concepts and technological innovation. It has strict standards and requirements for the treatment of waste tires. Pyrolysis tyre to oil technology just fits the strategic goal of sustainable development in Europe and has broad development space.
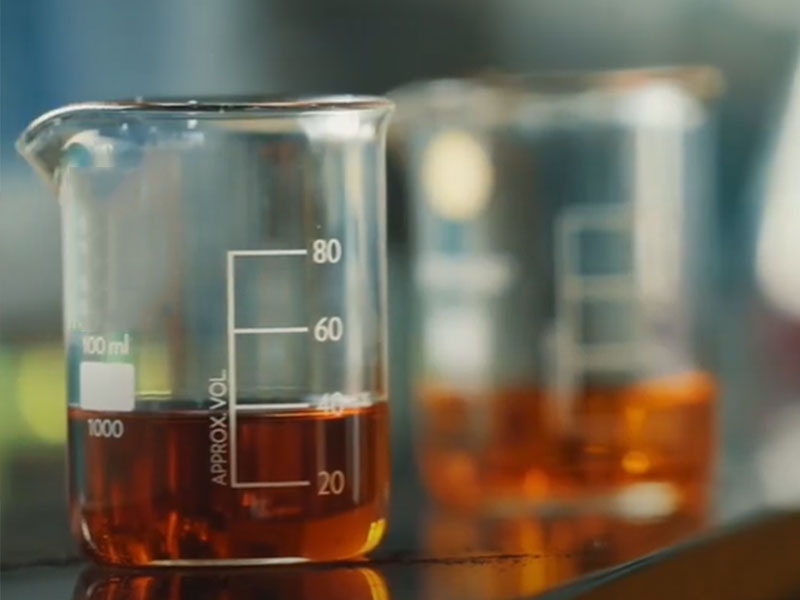
Application of Tyre Pyrolysis Oil
Tire pyrolysis oil has a high calorific value. After simple treatment, it can be directly used as an industrial fuel in multiple industries. In the process of steel smelting, high-temperature pyrolysis oil can provide sufficient heat for the furnace. In the field of cement production, pyrolysis oil can replace traditional fuels, provide heat for cement kilns, and reduce production costs.
Tyre pyrolysis oil can be used as a raw material to participate in the processing of tyre oil to diesel. Through processes such as distillation and hydrogenation, pyrolysis oil can be separated into different fractions to produce gasoline and diesel products. This not only enriches the raw material sources of refineries, reduces dependence on traditional crude oil, but also improves the economic benefits of refineries. Some large enterprises have begun to use pyrolysis oil as a supplementary raw material on a large scale. They optimize the process, reasonably mix pyrolysis oil with crude oil, and produce high-quality oil products that meet national standards.
The pyrolysis oil contains a variety of organic compounds, such as benzene, toluene, xylene and other aromatic substances, which are important chemical raw materials. In the chemical industry, pyrolysis oil can be used to produce synthetic materials such as plastics, rubber, and fibers. In the field of synthetic rubber, certain components in pyrolysis oil can be used as rubber plasticizers or modifiers to improve the performance and quality of rubber.
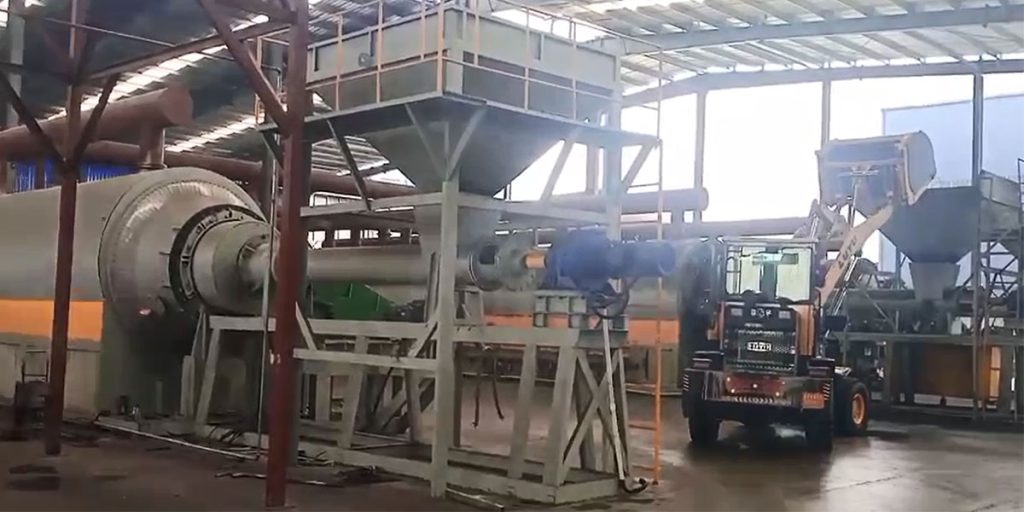
Pyrolysis Plant Manufacturer
As a professional pyrolysis plant manufacturer focusing on organic waste pyrolysis technology, Mingjie Environmental Protection is committed to providing customers with efficient and environmentally friendly waste resource solutions. The tire to oil pyrolysis plant can convert waste tires into fuel oil, carbon black, steel wire, and synthesis gas.
Compared with the mechanical recycling equipment for waste tires, the continuous pyrolysis equipment is extremely outstanding in terms of economy and environmental protection. It uses advanced continuous tire to oil pyrolysis technology to achieve deep resource utilization.
Mechanical recycling and processing of high-value components (steel wire, large-particle rubber) achieve rapid conversion with low energy consumption. Tire to oil pyrolysis technology digests low-value rubber powder and creates higher economic and environmental benefits through chemical reconstruction.
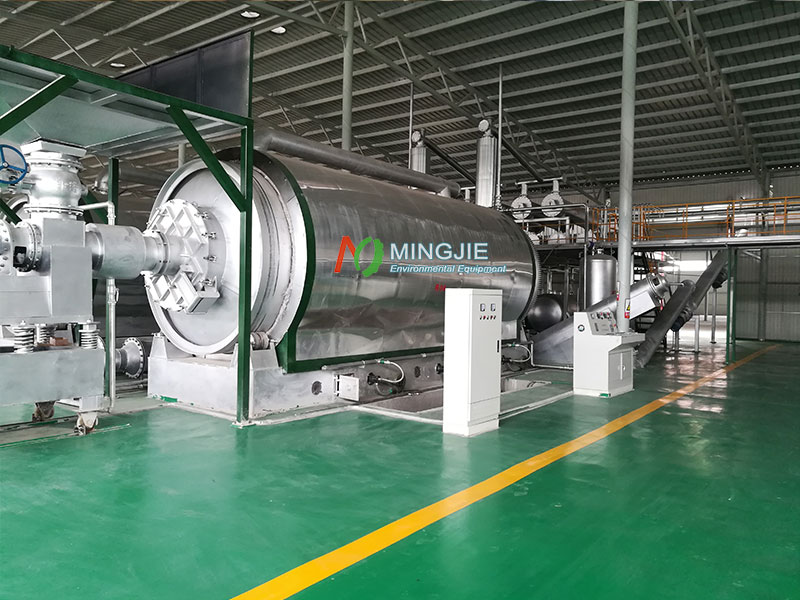
Fully Continuous Plant for Tyre Recycling
The fully continuous tire to oil pyrolysis plant consists of eight modules: automatic feeding system, continuous pyrolysis reactor, non-condensable combustible gas purification system, liquid separation cooling system, circulating cooling water system, flue gas purification system, automatic discharging system, and PLC fully automated control system.
After pretreatment, waste tires continuously enter the core cracker. Under the control of advanced intelligent control systems, waste tire rubber powder is heated more evenly under large disposal conditions, and product conversion can be completed quickly.
At the same time, the fully automatic tyre pyrolysis plant is equipped with an advanced waste heat recycling system. The non-condensable combustible gas produced can be used as fuel after purification, and the waste heat of high-temperature flue gas is also reused simultaneously. This makes heat utilization more fully, greatly improves pyrolysis efficiency, and achieves energy saving, carbon reduction, and consumption reduction.