Tire pyrolysis technology provides an effective way to solve the problem of waste tire treatment. It can convert waste tires into products with economic value, such as pyrolysis oil, carbon black, syngas and steel wire, and realize the recycling of waste resources. More and more investors are turning their attention to the field of tire pyrolysis plants. However, before making an investment decision, the tyre pyrolysis plant cost is a key factor.
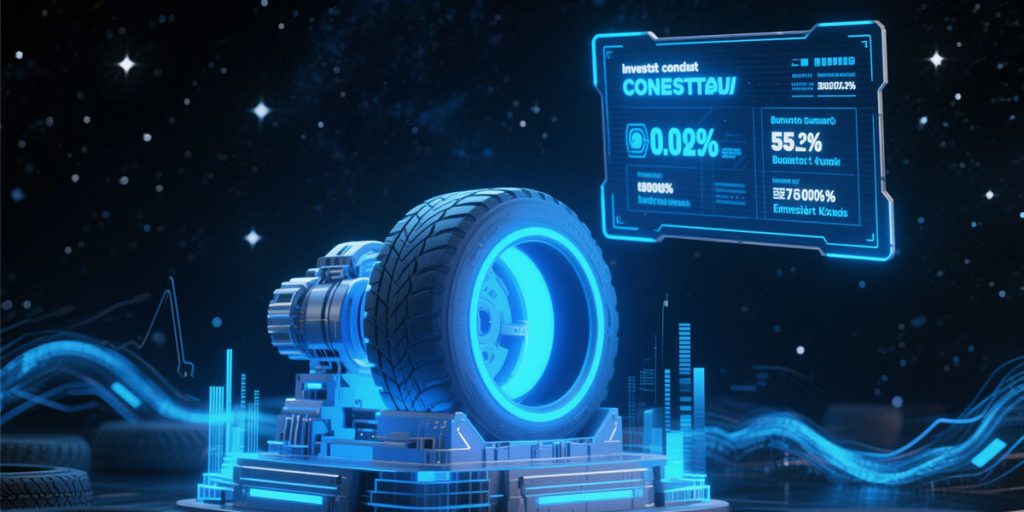
How Much Money Does It Take to Build a Tyre Pyrolysis Plant?
The tyre pyrolysis plant cost is a key factor. It is related to the initial investment, and closely related to the ROI and tire pyrolysis project sustainability. Therefore, it is of great practical significance to deeply explore the tyre pyrolysis plant cost, which can provide decision-making basis for investors.
It is hoped that it can help them make adequate preparations before entering this industry and avoid potential risks. In this way, they can seize the initiative in the tire pyrolysis recycling market and maximize the economic and environmental benefits of tire pyrolysis projects.
Tyre Pyrolysis Plant Cost
The small tyre pyrolysis plant cost is relatively low, ranging from 20,000 to 50,000 US dollars. The small pyrolysis equipment has a simple structure and adopts a skid-mounted design. The daily processing capacity of tires is 1-2 tons.
A batch tire pyrolysis plant has a daily processing capacity of 6-15 tons of tires. Batch Tyre Pyrolysis Machine Cost is between 50,000 and 500,000 US dollars.
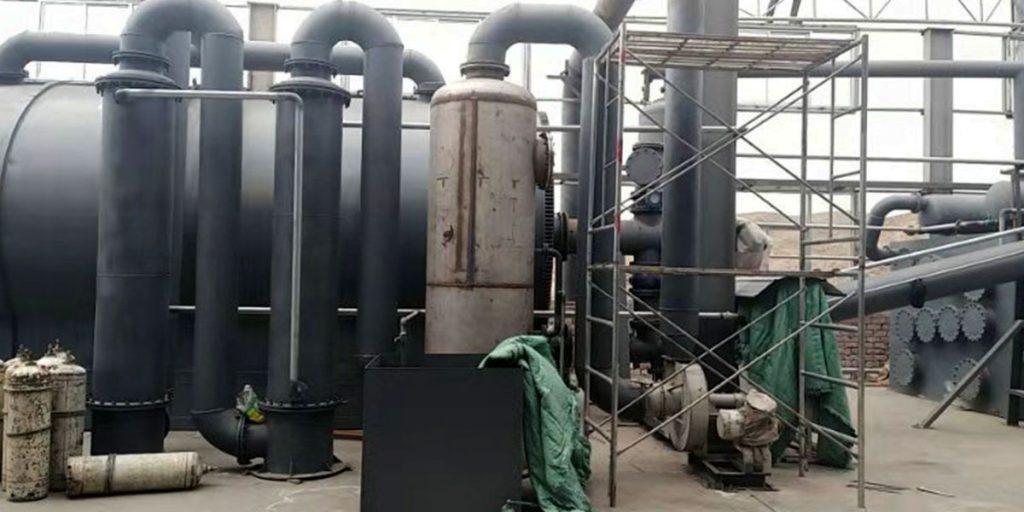
The configuration of batch pyrolysis plant is more complete, including efficient pyrolysis reaction equipment, condensation system, automatic spiral slag system and tail gas treatment system. Batch tire pyrolysis plants can achieve relatively stable commercial production and have certain competitiveness in the market. Batch pyrolysis equipment is a common choice for many companies to enter the tire pyrolysis industry.
A fully continuous tire pyrolysis plant can process up to 40 tons of tires per day. The fully continuous tyre pyrolysis plant cost is more than $5000,000. A fully continuous tire pyrolysis plant uses advanced continuous pyrolysis system, automated control system, and more environmentally friendly and efficient equipment. Fully automatic pyrolysis plants can improve production efficiency and product quality while reducing unit production costs.
Factors Affecting Tire Pyrolysis Plant Cost
The tyre pyrolysis plant cost is mainly affected by many factors, such as processing capacity, pyrolysis equipment material, degree of automation, and emission requirements.
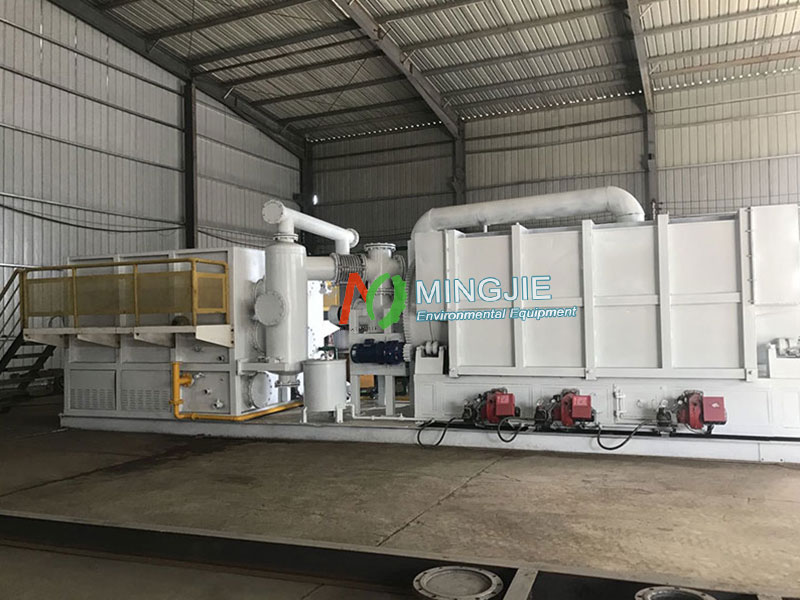
(I) Processing Capacity of Waste Tires
Processing capacity is one of the core factors that determine the waste tyre pyrolysis plant cost. The size of the capacity is directly related to the size and number of pyrolysis equipment, which in turn affects the equipment procurement cost.
Small tire pyrolysis equipment is relatively simple, equipped with a basic pyrolysis reactor and a simple cooling and separation device. Some small start-ups will choose to build small pyrolysis plants in order to initially explore the market. Although the capacity of small-scale pyrolysis equipment is limited, the initial investment cost is low and the risk is relatively controllable.
Medium-sized factories process 10-50 tons of waste tires per day, and need to be equipped with larger and more efficient equipment. Such as pyrolysis reactors with stronger processing capacity, oil separation systems with higher automation, and more complete tail gas treatment systems. While meeting certain market demands, they also need to invest more in equipment and technology to ensure production stability and product quality.
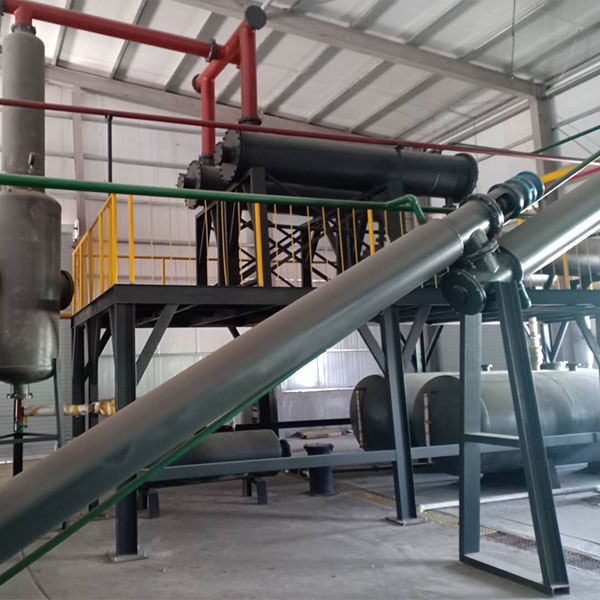
Large-scale factories process more than 50 tons per day. To achieve large-scale and efficient production, they usually use fully continuous pyrolysis plants. With advanced automatic control and monitoring systems, they can ensure accurate control and efficient operation of the production process. In addition, they also need to be equipped with large-scale raw material storage and transportation equipment, complete refining system and packaging equipment.
(II) Pyrolysis Technology
The type of pyrolysis technology has a significant impact on the tyre pyrolysis plant cost. Currently, there are two main types of pyrolysis technologies on the market: batch and continuous.
The structure of batch pyrolysis equipment is relatively simple, and the initial equipment procurement cost is low. However, this technology has many disadvantages, such as the discontinuous production process. It requires frequent operations, such as feeding, discharging, and cooling of pyrolysis reactor. This leads to low production efficiency and high labor costs.
Continuous pyrolysis plant has a high degree of automation and can achieve 24-hour uninterrupted production, greatly improving production efficiency. However, the investment cost of fully automatic tire pyrolysis plant is relatively high. However, from a long-term operation perspective, continuous technology can effectively reduce the production cost of each unit product due to its high production efficiency and low unit energy consumption. At the same time, it reduces labor costs and environmental protection costs, and has a higher cost-effectiveness.
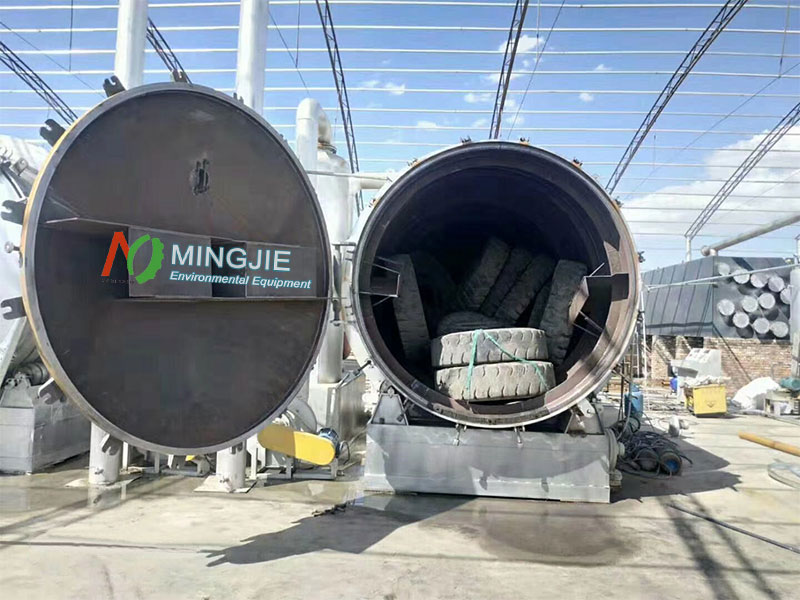
(III) Quality of Pyrolysis Equipment
The quality of pyrolysis equipment is another key factor affecting the tyre pyrolysis plant cost. Take the pyrolysis reactor as an example. It is usually made of high-quality high-temperature resistant and corrosion-resistant stainless steel. The price is 30% – 50% higher than that of reactors made of ordinary materials.
However, during use, it can reduce the loss of production suspension caused by equipment damage, and reduce the cost of repair and replacement of parts. In addition, high-quality pyrolysis equipment has higher energy utilization efficiency and can reduce energy consumption costs. From the perspective of the entire life cycle, it can save a lot of costs for enterprises.
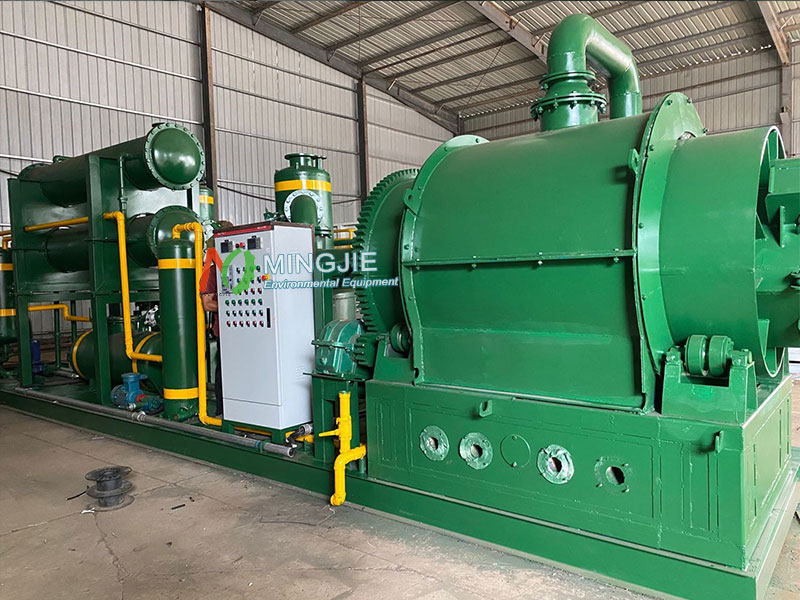
(IV) Customized Personalized Needs
If investors have special production needs, such as processing special types of tires, special requirements for product quality, or limited site space that requires specially designed equipment, customized equipment is needed. Customized pyrolysis equipment requires special research and development and design, and may use special materials and processes. The customized waste tyre pyrolysis plant cost will be 20% – 50% higher than that of standard equipment.
For example, some companies need to process waste tires containing special additives. Ordinary pyrolysis equipment cannot meet their pyrolysis requirements, so they need to customize special pyrolysis equipment. This not only increases the research and development and production costs of pyrolysis equipment, but may also lead to longer delivery cycles.
Conclusion
The tyre pyrolysis plant cost is affected by a combination of factors, such as capacity scale, technology type, equipment quality, and customization requirements. When considering investing in a tire pyrolysis plant, investors should not only focus on the initial investment cost, but should conduct a comprehensive and in-depth cost-benefit analysis.
It is recommended that investors conduct in-depth market research and fully communicate with professional pyrolysis plant suppliers and industry experts before investing. In this way, accurate cost data and industry information can be obtained, and a reasonable investment budget and operation plan can be formulated.