The small tyre recycling plant adopts a skid-mounted design and occupies a relatively small area. It is very suitable for layout in small and medium-sized cities or industrial parks. However, although it is small, it has all the necessary parts, covering all systems from waste tires to final product output. The small tyre recycling plant mainly includes pyrolysis reactor, heating system, cooling system, gas-liquid separation system, purification system and control system.
Pyrolysis technology is one of the important means for small tyre recycling plants to treat waste tires. It heats waste tires at high temperatures in an oxygen-free or low-oxygen environment to cause thermal decomposition reactions. Thus, tires are converted into usable resources, such as tire pyrolysis oil, carbon black, steel wire and combustible gas.
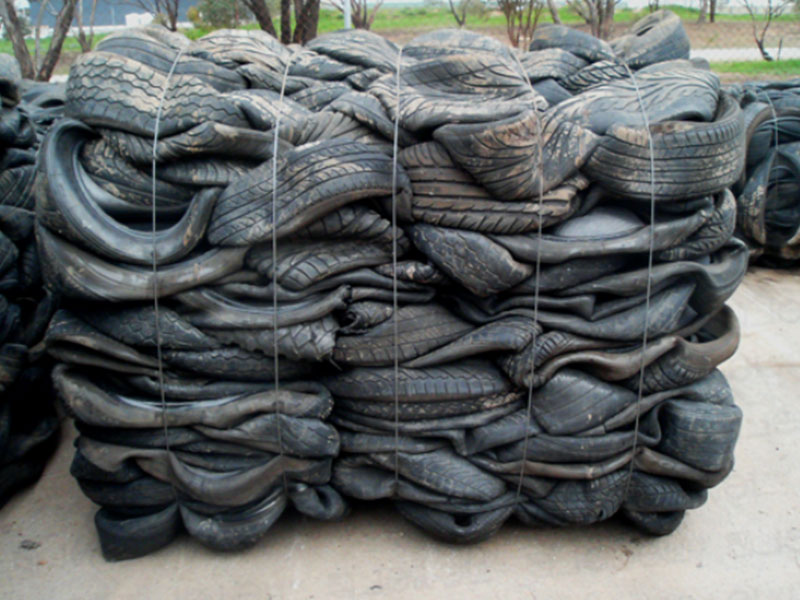
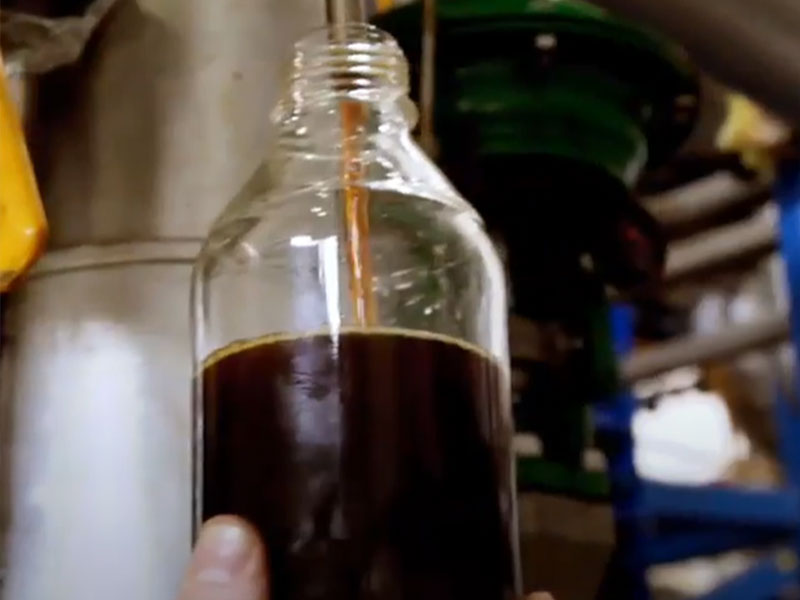
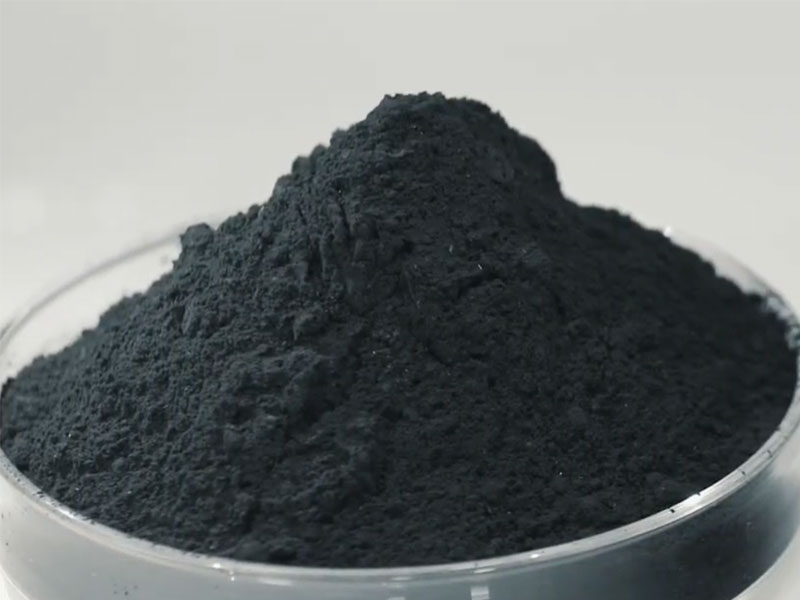
The small pyrolysis tire recycling system can process various types of waste tires, including car tires, truck tires, motorcycle tires, bicycle tires, etc. It converts waste tires into pyrolysis oil, carbon black, syngas and steel wire.
As a key tool for resource processing of waste tires, small tire pyrolysis plant plays an important role in solving environmental problems and realizing resource recycling.
Advantages of Small Tire Recycling Plant
In terms of environmental protection, the small pyrolysis equipment fundamentally solves the pollution problem caused by traditional treatment methods. It converts waste tires into reusable resources through pyrolysis reaction. This reduces the pollution of waste tires to land, air and water resources, and truly realizes the harmless treatment of waste tires.
In terms of resource utilization, the small pyrolysis tire recycling system achieves efficient conversion of resources. Each ton of waste tires can produce about 40% – 50% fuel oil, 30% – 40% carbon black, and about 10% steel wire and combustible gas through pyrolysis. These tire pyrolysis products have high economic value.
In terms of economic benefits, the operation of small tyre recycling plant can bring considerable benefits. On the one hand, the treatment of waste tires can obtain environmental protection subsidies from the government. On the other hand, tire pyrolysis oil TPO and recycled carbon black rCB have stable demand in the market, which can create continuous economic income for enterprises.
Development of Tire Pyrolysis Plant
Although the small tire pyrolysis plant is relatively mature, there are still certain bottlenecks in pyrolysis product quality control. In addition, the automation level of the skid-mounted small pyrolysis plant needs to be improved. It adopts batch pyrolysis, which affects the production efficiency of tire pyrolysis oil and recycled carbon black.
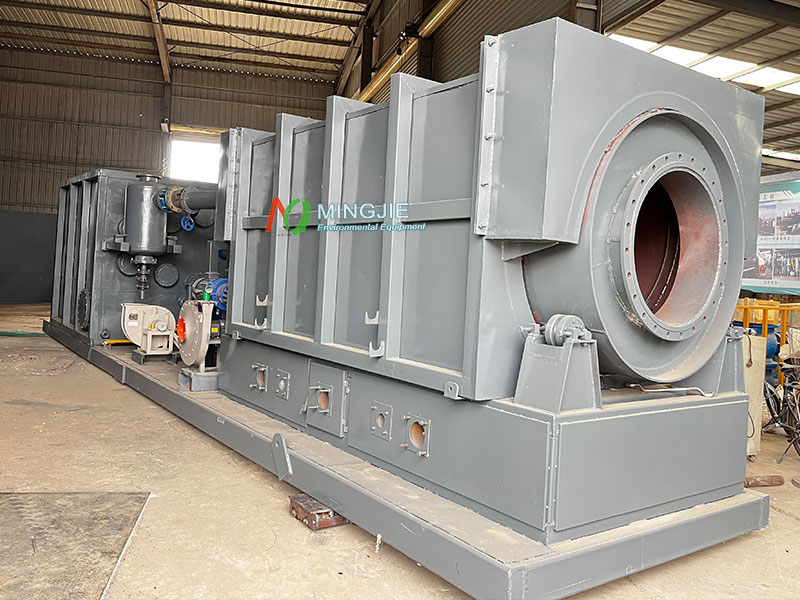
Skid-Mounted Pyrolysis Plant
Small skid-mounted tire pyrolysis equipment can be regarded as the prototype of pyrolysis technology. The pyrolysis system is installed on a movable skid-mounted base to meet the flexible deployment needs of small sites.
The limitations of this equipment are very obvious. The single batch processing capacity is only 1-2 tons, and a maximum of 3 batches of production can be completed per day. The manual feeding and slag removal process is labor-intensive.
Semi-Continuous Batch Pyrolysis Plant
With the increasing environmental protection requirements and the pursuit of efficiency, batch pyrolysis plant has begun to incorporate preliminary automation elements. The batch pyrolysis equipment has introduced a PLC control system that can automatically adjust the heating power.
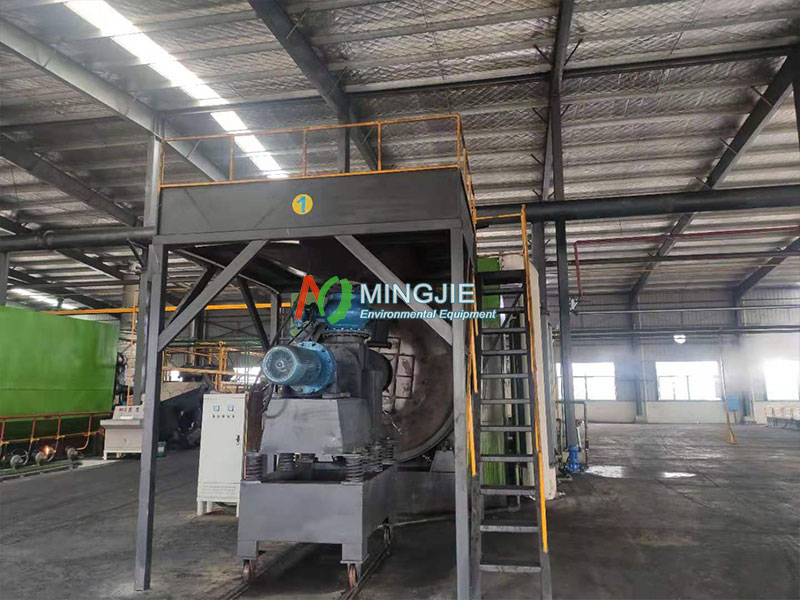
A hydraulic auxiliary feeding device has been added to the feeding link, and a water-cooled spiral slag discharge device is used at the discharge port. At the same time, the condensation system has been upgraded to a shell-and-tube heat exchanger, and the pyrolysis oil recovery rate has been increased to 40%-45%. A simple exhaust gas combustion device has been installed to directly ignite and treat the non-condensable gas to reduce odor emissions.
Each batch of production still needs to go through the complete cycle of loading – heating – cooling – unloading, and the maximum daily processing capacity has only increased to 8-10 tons. Carbon black cleaning, equipment maintenance and other links still rely on manual labor, and it is impossible to maximize the energy utilization brought by continuous feeding.
Fully Automatic Tire Pyrolysis Plant
With the maturity of industrial Internet of Things and equipment manufacturing technology, small skid-mounted tire pyrolysis equipment has achieved a qualitative breakthrough. The continuous pyrolysis plant adopts a modular design, integrating five modules: fully automatic feeding system, intelligent temperature control reactor, continuous discharging device, exhaust gas purification system and central control system.
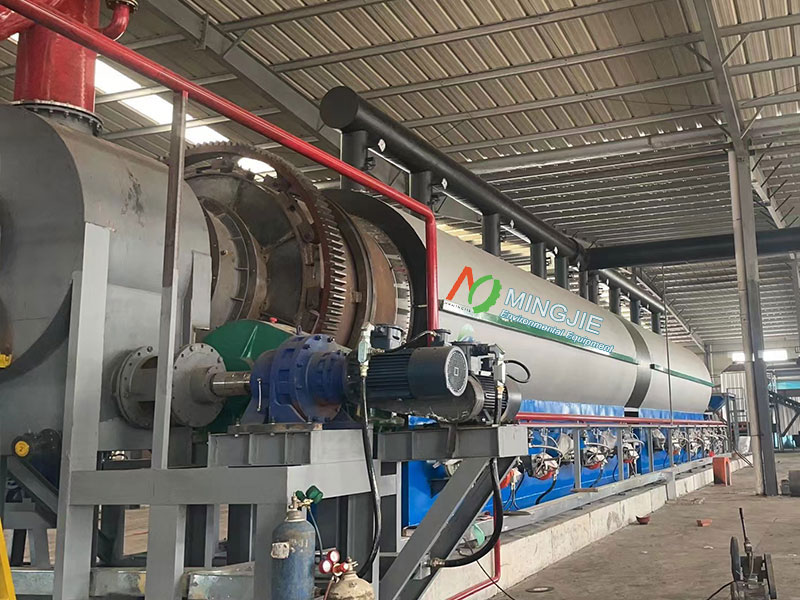
Waste tires need to be processed by removing steel wire and crushing. The raw materials need to be crushed into rubber powder without steel wire. The raw materials are fed into the reactor by the feeding system at a set rate. This allows 24-hour uninterrupted feeding.
The stainless steel reactor uses double-layer insulation technology to ensure that the tire rubber undergoes stable and rapid pyrolysis reaction. The oil and gas produced by pyrolysis automatically flow into the oil storage tank after multi-stage condensation separation. After desulfurization and denitrification, part of the non-condensable gas is recycled into the heating system, achieving an energy self-sufficiency rate of more than 60%.
The continuous tire pyrolysis plant uses a water-cooled spiral seal discharging device to continuously discharge carbon black residue. After magnetic separation of steel wire, the carbon black directly enters the grinding system to be processed into finished products. The central control system displays the equipment operating parameters in real time through the touch screen, and can remotely monitor and automatically warn of faults.
The transition of the tyre recycling plant from batch to fully automatic is not only an upgrade of equipment technology, but also a reconstruction of the industrial model of waste tire recycling. The tire pyrolysis plant has become a large-scale, standardized and environmentally friendly solid waste treatment equipment.